Research for energy system transformation
Highly complex, extremely flexible test air supply system from AERZEN for energy research. The test air supply system of AERZEN meets the highest requirements for controllability, measuring accuracy, flow quality, repeatability and constancy. AERZEN has built a test air supply system for the new research building “Dynamics of Energy Conversion” at the Leibniz University of Hanover, which is unrivalled in terms of precision, dynamics, complexity and size, and places the energy technology research facility in Garbsen among the top 10 worldwide.
Renewable energy is the future and good for the climate but creates special challenges for conventional power plants. This is because sun and wind are not always available, and fluctuate according to weather conditions, time of day and season. The consequence is peak loads and undersupply. However, existing power generation plants are not designed for such fluctuations. In order to ensure security of supply and system stability in the future, power plants must operate more dynamically and guarantee fast start-up and efficient partial load behaviour.
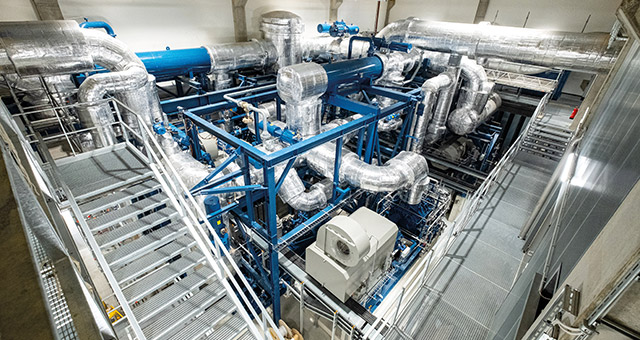

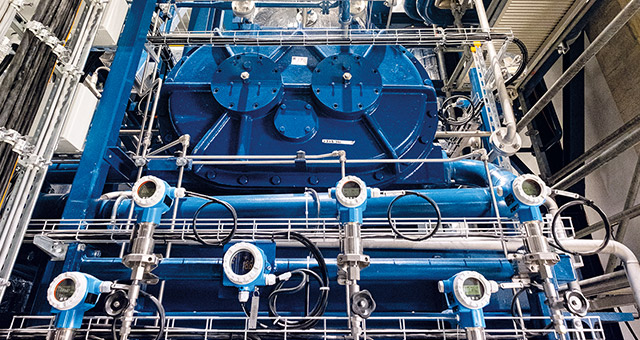
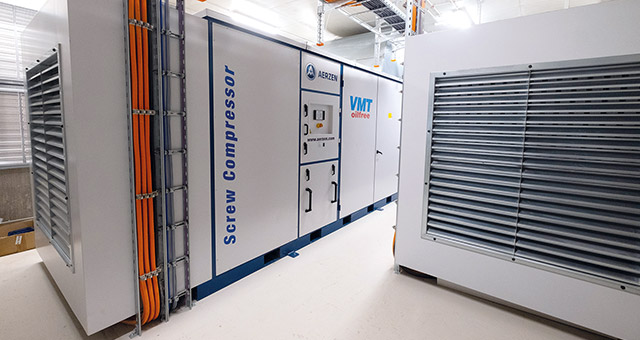
Solutions for energy system transformation
But how do power plant components behave under changing loads? The Institute of Turbomachinery and Fluid Dynamics (TFD) at the Leibniz University of Hanover (LUH) deals with questions like this. Since September 2019, one of the world’s most modern research facilities is available to scientists for this purpose. The new research building “Dynamics of Energy Conversion” (DEW) of the research association of the same name is home to approximately 2000 square meters of test benches for experiments on turbomachinery and power plant components such as motors, generators, turbines, diffusers and compressors, and enables tests of up to 6 MW. Therefore, the facility closes the gap between typical university laboratory experiments, which generally have a power output of only a few hundred kilowatts, and the testing of industrial prototypes with many hundreds of megawatts. The total investment volume for the Mechanical Engineering Campus amounted to €175 million.
Energy technology research at a new level
The heart of the building, on the newly opened Mechanical Engineering Campus in Garbsen, is the large compressor station made by Aerzener Maschinenfabrik GmbH. The plant supplies the individual test benches with compressed air and meets the highest requirements for controllability, measuring accuracy, flow quality, repeatability and stability. “Research into complex flow phenomena in high-performance turbomachines requires technologies that can precisely provide and repeat inlet and outlet conditions and mass flows. This is the only way to achieve the flow speeds and stage pressure ratios found in modern turbomachines as realistically as possible,” explains Dr. Hans-Ulrich Fleige, Head of R&D at AERZEN, and adds: “With our test air supply system, the test benches can be operated dynamically with almost freely selectable load ramps and investigations can be carried out under high load gradients over wide operating ranges. To generate aerodynamic similarity between reality and model test, both Mach and Reynolds number can be adjusted - independently of each other. The actual operation of existing and future turbomachines can therefore be optimally modelled.” Thanks to the new possibilities, the TFD and the energy technology research at Leibniz University are among the top 10 leading research centres in the world in this field.
Successful premiere: Blower specialist as plant manufacture
For over 150 years the name AERZEN stands for innovative, efficient compressor technology that is precisely tailored to the respective process. For Garbsen, the application specialists not only supplied the blower and compressor packages, but also appeared for the first time as plant engineers and were responsible for the design, planning, manufacture, assembly and commissioning of the entire plant, including the measurement and control technology. The business unit Special Purpose Machine Construction (Process Gases) was in charge of the development and construction in close cooperation with LUH and the TFD. They were supported by a multitude of external and internal partners, including Emmerthaler Apparatebau, Kratzer Automation, AERZEN After Sales Service and the AERZEN R&D Group.
Maximum precision and flexibility
The test air supply system (total dimensions: 82 x 15 x 9 m.) comprises a compressor station with a multi-stage compression, a cascaded bypass for fine control of the mass flow rate, a central mass flow rate measuring section, an air distribution system to and from the test benches including piping, valves, silencers, coolers, settling chambers and supporting steel structure as well as a sophisticated control system for selecting different operating modes, types, configurations and test bench inlet conditions.
The test benches work with expansion ratios between 1 and 6. The inlet pressure ranges from 1 to 8 bar (abs) with a maximum mass flow rate of 25 kg/s (90000 kg/h). Under all conditions, the inlet temperatures can be controlled between 60 and 200°C. The system can be operated in both open and closed loop modes, is designed for steady as well as transient (± 30% of the maximum volume flow rate per minute) operation and can be either pressure or mass flow controlled. Volume flow rate, temperature and pressure are freely definable and can be regulated independently. To achieve the desired flexibility and dynamics, and in particular to meet the requirement for extreme accuracy, the AERZEN engineers were driven to deliver technical high performance. For example, the deviation of the volume flow is just 0.015 m³/s - and that with an effective maximum value of up to 80000 m³/s. The average static pressure can be set to an accuracy of 0.5 millibar and the average static temperature fluctuates by a maximum of 0.3 K, to give just a few examples.
Make 5 out of 1
The central mass flow rate measurement unit is also unparalleled, with a total uncertainty of only 0.55 percent. “The control requirements were higher than the inaccuracies of normal measurement technology,” emphasizes Jens-Olaf Wittenberg, Project Manager Supply Process Gas at AERZEN. The test air from the supply line in DN 700 is distributed via a diffuser to five parallel ultrasonic gas meters (4 x DN 500 and 1 x DN 200). The number of active lines depends on the flow rate and is automatically regulated by the control system, so that all gas meters are operated with the lowest measurement uncertainty. In order to achieve an even distribution of the flow to the individual measuring sections and uniform velocity profiles at the gas meters, flow rectifiers were provided upstream of the individual gas meters and the diffuser including the upstream pipe bends was flow simulated. In addition, vortex generators are installed at the diffuser inlet and special components are fitted to reduce the outlet area. Splitting of the mass flow rate measurement became necessary due to the size of the project. “There was simply no transportable gas meter available in DN 700 for the in-situ calibration which was required by the TFD,” says Jens-Olaf Wittenberg.
Multi-Stage compression
The thermodynamic treatment of the test air is carried out in the compressor station (total size: 27 x 15 x 9 m.). As a first stage, this uses two parallel-connected Roots blowers of type GM 20.20, each with an inlet volume flow between 9600 and 48600 m³/h and a maximum pressure difference of 0.8 bar (inlet pressures between 0.2 and 3.5 bar, max. outlet pressure: 4.3 bar). The second stage consists of two parallel screw compressors type VRa 736 S with an inlet volume flow between 6900 and 21600 m³/h and a maximum pressure difference of 10 bar (inlet pressures between 0.2 and 3.5 bar, max. outlet pressure: 9 bar). All four machines are driven by separate electric motors (690 V) with speed control and can be operated at variable speeds in single or tandem operation. “Due to its modular design, the compressor station is extremely flexible and has an extraordinarily large control range,” Dr. Hans-Ulrich Fleige makes clear, and adds: “Low pressures are taken over by the positive displacement blowers, for medium pressures the screw compressors start up and high pressures can be achieved with a two-stage operation of the blower and screw compressor.”
AERZEN has paid special attention to sound insulation. All four compressors have two reactive silencers; the positive displacement blowers are additionally equipped with two lambda quarter resonators. This largely reduces pulsations and their effects. “The large control range results in an enormously wide frequency spectrum. It was a bit of a challenge to get a grip on the sound,” admits Dr. Hans-Ulrich Fleige. In order to protect the surrounding research buildings, where, among other things, highly sensitive acceleration and vibration tests are carried out, the machine foundation was completely decoupled from that of the compressor room.
Perfection down to the smallest detail
A special feature of the system is that it was completely integrated into an existing building. The challenge was to deal with the limited space available and the already fixed statics of the building. For example, around 190 tons of steel beams were used to dissipate the resulting forces. In addition, virtually all components and parts of the system were specially designed and manufactured - starting with the mass flow measuring section, the diffuser and the settling chambers in front of individual test cells. Even the pipelines - a good 500 metres in total (from DN 200 to DN 1000) - and most of the pipe bends are anything but standard. Elaborate flow simulations and improved corrosion protection thanks to galvanisation are just a few of the points that make the difference here.

The two-year construction phase was preceded by a multi-year planning phase by the engineers from AERZEN and Hanover. Due to the demanding requirements regarding stability and reproducibility of the test air, a fully functional scaled model with a power of 300 kW was built for pre-testing the measurement and control technology. “We have many years of experience in the field of process gas technology, but this project was something special - and not just because of its size and complexity,” says Jens-Olaf Wittenberg.
“For the first time, we were able to demonstrate our plant engineering competence in the field of special purpose machines, and that right away with a project of this magnitude. After all, this is the largest domestic order in the history of our company.”
Lower Saxony’s Minister President Stephan Weil successfully started the first run at the campus inauguration in September 2019. Final commissioning will follow in 2020.