Process Gas Technology
Individual and Reliable Processes
Where gases are compressed in highly-critical processes, there are few tolerances. Process gas solutions must meet highly specific requirements. Just as strict laws and guidelines. Above all, they must ensure one thing: A reliable, uninterruptible and economic production process. Under any conditions. In all applications, industries, and countries of the world. AERZEN offers the process gas industries an enormously broad spectrum of blower and compressor technologies – perhaps the broadest of all. The machines work in all industrial key applications on a stand-alone basis, in machines or containers, onshore and offshore.
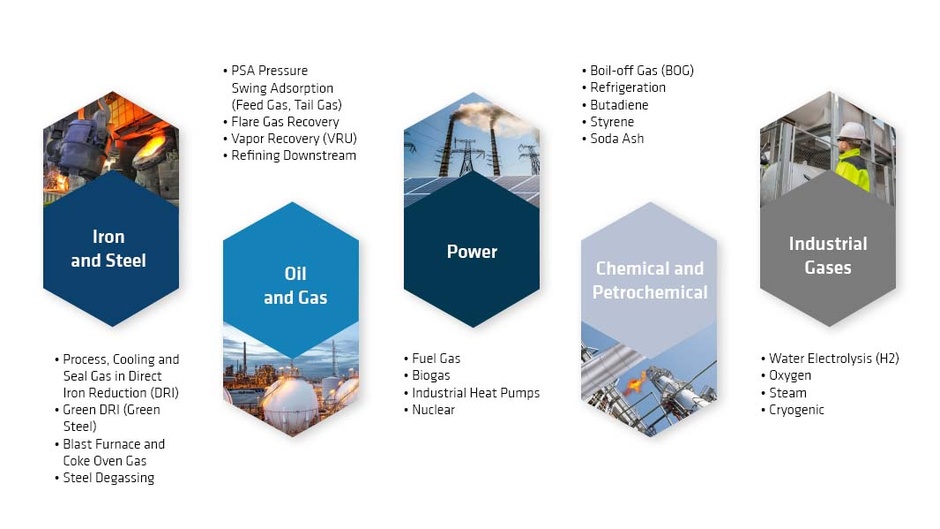
Information & documents
Suitable Products
for Process Gas Technology
Process Gas compression and conveyance
The company has also been delivering blowers and screw compressors for special applications in the process gas industry for around 60 years. Since then, AERZEN has developed into one of the most competent suppliers for technical solutions in process gas applications. The team is made up of experienced experts from the fields of construction, instrumentation/control systems, sales, application and project management. The process gas specialists predominantly work in the USA, Germany, Hungary and India and are closely connected – This cross-country network of experts focuses on the special knowledge related to the application of positive displacement blowers and screw compressors in the process gas and refrigeration industry. For planning and engineering, the team has the latest software tools at its disposal, such as Auto CAD, Engineering Base for flow diagrams and bill of materials, or UNISYM for the process calculation. 3D visualisation and precise material lists provide transparent alignment with the customer for each stage of planning.
This allows us to develop bespoke solutions for the widest range of applications in close cooperation with our customers. We have already installed approx. 2,000 plants around the world.
Supply process gas – Analysis and project support
Individual consulting is provided before a process gas plant is purchased or installed. This comes with a detailed analysis of the customer's initial conditions and the creation of a requirements profile for the future plant. The data to be collected includes the composition of the gas that needs to be compressed or conveyed, the intake and desired discharge pressure, conveying volumes, environmental conditions and the available cooling water flow – all these steps are carried out in close cooperation with the customer.
The process gas team subsequently accompanies the customer in all phases of the project – from planning to project management, right up to the itemized list and commissioning, certification and documentation. Complex package unit control systems are also part of the AERZEN portfolio, which are incorporated into the existing customer systems. Generally, redundant connections and process validations are generally included. Depending on the type of application and results of the risk analysis, safety-related control systems according to the safety integrity level (SIL) are an elementary component of the system architecture.
By cooperating with AERZEN, the unique expertise of a leading manufacturer in the field of compressed air and process gas handling gives a crucial advantage to the customer, since the long-standing experience of the company flows together in every consulting and planning stage.
Service solutions for comprehensive repairs and modernisations
AERZEN process gas machines are designed for continuous operation. If unexpected faults do occur, specially trained technicians provide round-the-clock support. In coordination with AERZEN After Sales, spare parts deliveries, repairs and overhauls can be prepared quickly and easily.
In addition to on-site services, AERZEN also offers in-house repairs at its headquarters. Here, the machine receives an all-round carefree package including detailed findings, in-house production and testing options for all products repaired in Aerzen. To reduce machine downtimes, AERZEN offers customised spare parts and replacement machines. This enables AERZEN to support the customer in selecting and scheduling the required components in the best possible way.
AERZEN Revamp
In cooperation with AERZEN, it is possible to modernise an entire plant or components of it. Whether automation, efficiency improvement or speed control. Depending on the requirements, a plant can be modernised from many different points of view with a focus on the maintenance of what is tried and tested and/or necessary. AERZEN has been working closely for years with partners in the field of 3D laser measurement in system manufacture for many years in order to record the current condition of ageing plants and utilise the findings. The replacement of necessary components or individual compressors and blowers takes place in the existing package! This results in a considerable reduction in investment costs, short downtimes and accurate and comprehensive documentation of the project.
Involve us in your planning! Please contact parts-service@aerzen.com
The compressor series VR is a module system for the dry compression of process gases. Of all of the process gas-specific products from AERZEN, these assemblies generally have the widest possible range of applications. They compress and convey virtually all industrially used gases such as ammonia, argon, ethylene, acetylene, butadiene, hydrogen chloride gas, natural gas, flare gas, furnace gas, mine gas, helium, lime kiln gas, coke oven gas, carbon monoxide, all hydrocarbons, methane, propane, propylene, flue gas, crude gas, sulphur dioxide, nitrogen oxide, nitrogen, styrene gas, vinyl chloride and hydrogen. The only limit to the range of applications in process gas compression comes from each of the allowable pressure, temperature and speed ranges or the liquid content in the conveying medium.
With a speed range of between 7,000 and 18,000 min-1, the series achieves an intake volume of up to 75,000 m3/h. The standard machines are able to work mechanically with a differential pressure of up to 12 bar. For special application cases, machines can also be manufactured with a load limit of up to 25 bar. In a multi-level version, final pressures of up to 52 bar g and vacuums of up to -900 mbar can be achieved.
With these high intake volume flows, high differential pressures and extreme discharge pressures, the series sets itself well apart from other compressors.
A special design feature makes the VR process gas compressor ideal for use in the chemical, petrochemical, pharmaceutical and food sectors: there is no metal contact in the rotor chambers – neither between the two rotors nor between rotors and the casing. This ensures an absolutely oil-free operation method, since the rotor chambers and therefore the conveying medium remain 100 percent pure.
Thanks to the modularity of the assemblies and flexible combination options with various accessories, the range of applications can be increased even further. The compressors can therefore also be used in control air systems, industrial refrigeration plants, evaporating plants, mining and steel works.
The cooling effect of the gas associated with the oil injection provides the VMY with a higher intake temperature compared to oil-free compression. For cleaning the process gas, oil separator systems are integrated as standard, reducing the residual oil content by up to >5 ppm(w).
Process gas compressor assemblies in the VMY series, like all twin-shaft displacement machines, are characterised by high flexibility compared to fluctuating operation or working conditions and volumes. They are equipped as standard with a slide control for the volume flow control. This enables a continuous adjustment of the volume flow between 100 and 20 percent.
The assemblies are particularly suited to the handling and compression of gases with light molecular weights and fluctuating compositions, such as inert and combustible gases, oil-consistent mixed and process gases, natural or inert gases as well as all standard coolants.
The products in the VMY series are available in 14 sizes with an intake volume flow between 190 and 23,000 m3/h and a pressure range of -0.9 to 25 bar (g).
The oil-free conveying process gas blowers from AERZEN are very durable power blowers. A continuous fluid injection for gas cooling and/or cleaning is possible thanks to existing sealing and ventilation hood connections. This is advantageous for contamination caused by uncleaned process air or process gas. Oil and rotor chambers are completely separated by neutral chambers. The process gas blowers are available in a very wide range of special materials. Both series also work according to the displacement principle and can adapt exceptionally well to changing operation or working conditions.
The degree to which air compressors have to function in line with processes is highlighted by the fact that compressing positive displacement blowers are used in nuclear power stations for compression of water vapour in secondary cycles.
The GR process gas blower series conveys and compresses, amongst others, hydrogen, methane and carbon monoxide mixed gas, water vapour and toxic gases with intake temperatures of up to -40° C. Its intake volume amounts to between 90 and 38,000 m3/h. The pressure range lies between -500 mbar and 6,000 mbar g. The differential pressure amounts to a maximum of 1,500 mbar. The direction of flow of the blower is vertical.
The GQ process gas blower series is used predominantly in the steel industry for handling coke oven gas and as a furnace gas blower. Compared to the GR, it has a larger intake volume flow. This ranges from 910 to 104,000 m3/h. As with the GR blower, the pressure range lies between -500 mbar and 6,000 mbar g. As with all blowers, the maximum differential pressure lies at 1,500 mbar. Apart from the larger intake volume, the main difference is the horizontal direction of flow. Conveyed mediums include air, inert, toxic, combustible, corrosive gases or mixed gases. Typical fields of application are steelworks, where blowers are used for the compression of process, coolant and sealing gas in DRI processes (direct reduction of iron). They are most commonly used in multi-stage assembly arrangements and, like all AERZEN process gas compressors, are extremely resilient against contamination in the gas, like tar and naphthalene, as well as fluctuating operation or working conditions.
The high pressure blowers in series GM-HP are suitable for applications in which high differential pressures are required. The assemblies have a differential pressure range of up to 2,000 mbar. This is necessary where the conveyed mediums such as air, inert or mixed gases come out of the pipe systems already with an elevated intake pressure.
The robust, directly driven, single or double-stage machines, like all blowers, work according to the roots principle and are available in numerous special materials and special seals. Depending on size, they produce an intake volume flow of 30 to 38,000 m3/h and retain an overpressure of up to 25 bar g. The maximum differential pressure amounts to 2,000 mbar.
Further information and specific application reports are available on our website Process gas and coolant industry.