Harinas Elizondo in Mexiko
Der mexikanische Mehlproduzent Harinas Elizondo setzt seit November 2010 den Drehkolbenverdichter Delta Hybrid zur pneumatischen Förderung der Rohstoffe ein – und konnte seine Produktion trotz der widrigen Umweltbedingungen um 54 Prozent steigern.
Ohne Druckluft stünden die Mühlen bei Harinas Elizondo still. Bis zu elf Tonnen Getreide und Mehl werden bei dem langjährigen Kunden der Aerzener Maschinenfabrik pro Stunde entweder zur Weiterverarbeitung oder zur Lagerung pneumatisch in Silos befördert – eine tägliche Herausforderung für die Systeme, die in Mexico City in einer Höhe von 2.250 Metern über Null arbeiten müssen. Der geringere Luftdruck beeinflusst nämlich die Effizienz aller mit Luft arbeitenden Maschinen, zum Beispiel auch von Automotoren: Im Vergleich zu baugleichen Geräten, die auf Höhe des Meeresspiegels betrieben werden, reduziert sich deren Leistung deutlich.
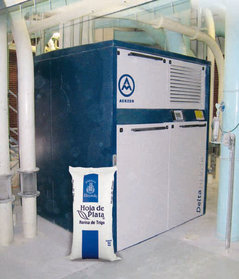
Was zählt, ist Qualität
Seit mehr als 60 Jahren ist die mexikanische Mühle mittlerweile im Geschäft. Ein Grund für den langjährigen Erfolg ist die hervorragende Produktqualität, die nicht nur aus den hochwertigen Rohmaterialien resultiert, sondern auch aus dem Einsatz neuester Technik. Basilio Gonzalez, technischer Direktor von Harinas Elizondo: „Nur wer in Qualität investiert, kann auf Dauer wirtschaftlich und zuverlässig produzieren und gleichzeitig den Kunden zufriedenstellen oder seine Erwartungen sogar noch übertreffen.“
Zur modernen Ausrüstung des Mehlproduzenten gehörte auch ein Aerzener Gebläse der Reihe Delta Blower, das dort zuverlässig viele Jahre lang im Einsatz war. Um die Kapazität des Systems zu erweitern und gleichzeitig Energie zu sparen und einen Beitrag für die Umwelt zu leisten, tauschte ein Team aus deutschen und mexikanischen Technikern das Gebläse im November 2010 gegen ein Aggregat der neuen Drehkolbenverdichter Baureihe Delta Hybrid aus.
Ziele übertroffen
Schon nach kurzer Zeit konnte Harinas Elizondo die Produktion steigern und sich die erhöhte Leistung in der Hochsaison zunutze machen. Heute fördert das System bei gleichem Energieverbrauch etwa 17 statt elf Tonnen pro Stunde – das entspricht einer Produktionssteigerung von 54 Prozent.
Damit wurden die ursprünglich gesetzten Ziele übertroffen: mehr Leistung, Energieeinsparung, hohe Zuverlässigkeit und Produktqualität sowie seltenere Wartungen. Ein Ölwechsel wird erst nach 16.000 Betriebsstunden durchgeführt und die Lebensdauer der Lager beträgt bis zu 60.000 Betriebsstunden.