Success Story - Milser Muehler
The mills grind efficiently
When the Borgstedt Family took over the Milser Mühle 130 years ago, at first, it only produced feed material, and then, from 1918, it started to produce flour for human food. “Therefore we selected oilfree compressing AERZEN Positive Displacement Blowers of series GM as conveying air producer for the closed piping systems. Until today we are only using AERZEN units“- says Mastermiller Friedrich-Wilhelm Borgstedt. These blowers are from several generations of the series, due tothe long operation period of the units.
“Today, pneumatic conveying is necessary for the economical operation of a modern mill company”, explains the senior chief. In the Mehlstraße, eleven AERZEN units have been working with a highest pressure from 650 to 750 mbar and driving power from 4 to 30 kW. According to Borgstedt, the relatively low pressure range is reached with the longer lifetime of the blowers, the locks and the pipings, and, in particular, the pipe bends. Seven AERZEN blowers, not of sound insulated design, are in a central station, with three further units, which are sound-insulated, located in an adjacent room.
The version without acoustic hoods was consciously selected in order to avoid contaminations as a result of vermin-nesting places – a widespread problem for mill technology. However, this means that considerable radiation heat is generated, as well as high noise levels. Consequently, sufficient fresh air has to be ensured for compression and cooling of the units. Due to the corresponding openings, however, noise does not escape from the station.
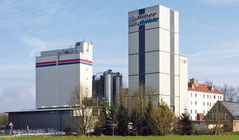
Factory building Milser Muehler
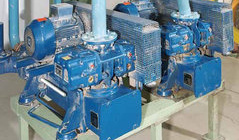
Milser Muehler Central Station
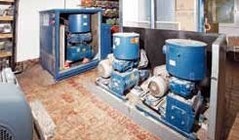
Sound insulation bonnet
Calculation of the optimal room ventilation
Using a special AERZEN online-tool, the so-called “room ventilation calculator”, the maximum required inlet air quantity, the ventilator power and the size of the wall openings were determined. In this calculation program, the installed type of machine must first be selected – in this case “Blower”, however, “Compressor“ or “Turbo Units“ may also be selected. The type of suction must then be defined – in the case of Milser Mühle, the options are: “room suction from outside of the room“, or “room suction out of the room“. The calculation is effected after input of the following information – the totally installed motor rating, the ambient temperature, the admissible temperature increase, the maximum intake volume flow of the whole station, the installation height and the flow velocity. The combination of this data produces precise findings which can then be used to determine the optimal solution. Although splitter silencers in the channels allow air to enter the station, the noise level outside the building is minimized.
In operation around the clock
Production at the Milser Mühle normally takes place behind the mills, from Monday mornings through Saturday mornings, prior to the cleaning work. In exceptional situations, production also takes place on Sunday mornings. Therefore, a reliable and fail-safe supply of conveying air is imperative for Borgstedt. Only then, – can the mill operate on as troublefree basis – an essential requirement for meeting the delivery dates agreed with customers.
However, such solutions for pneumatic conveying concepts in the food industry are not – “ready-made“ –. In the preliminary stages of such an investment, a detailed specification has to be compiled. AERZEN supplies the AERZEN Positive Displacement Blowers of the series Delta Blower – “Generation 5“ – tailor-made for all ranges of application in the pneumatic conveyance including all standard accessory components for effective operation at the push of a button. They can be used in all climates and will work in the most difficult ambient conditions just as safely as they will in a hall installation – reliably, durably and energy-efficiently. As an option, AERZEN blowers can also be supplied in ATEX-design according to EU-guideline 94/9/EC. This is an increasingly important criterion not only for the food industry, but also for many other branches of industry such as the synthetics industry, environmental technology, the chemical and pharmaceutical industries, in refineries and in power plant technology.
Friedrich-Wilhelm Borgstedt, Senior chief Milser Mühle:
„We would always decide on AERZEN. Our main reasons for doing so are the high quality and reliability of the units, their longevity as well as the geographic proximity of the manufacturer.“