Screw Compressors
Oil-injected single-stage Screw Compressor
Series SI
Thanks to an innovative screw compressor stage and a highly efficient class IE5 permanent magnet motor, the single-stage, oil-injected compressed air packages in the SI series achieve a very high energy efficiency level - even in partial load operation. This enables significant energy savings in compressed air generation and contributes significantly to economical, resource-saving and sustainable processes
Volume flow:
17
to
726
m3/h
Differential pressure (Δp):
5.500
to
13.000
mbar
Medium:
Air,
Neutral Gases
Compression:
Oil injected
The advantages of AERZEN Screw Compressors Series SI at a glance:
- Maximum energy efficiency - even in partial load operation
- Reduced investment costs due to the extensive eligibility for subsidies based on the BAFA subsidy programmes
- Extended volume flow control range by integrated VFD technology
- Unrivalled reliability thanks to an innovative package design
- Secure use in extreme environmental conditions and with the most difficult requirements
- Maximum noise reduction thanks to innovative package design
- Reduced service costs due to extended maintenance intervals and roller bearings in PM motors being no longer required
- Compact design leads to a very small footprint
As diverse as your applications
Compressed air is omnipresent in industry and has become indispensable in many applications - be it in chemical/ petrochemical process technology, electronics and
semiconductor production and many other areas.
Read more
US Units
No- Type of technology
- Screw Compressors
- Design
- Positive pressure
- Differential pressure (Δp)
- 5.500 to 13.000 mbar
- Volume flow
- 17 to 726 m3/h
- Medium
- Air, Neutral Gases
- Compression
- Oil injected
Outstanding energy efficiency
- Significant energy savings, achieved through extremely high efficiency in the compressor stages, in connection with the highly efficient PM motor, offering an energy efficiency of approx. 96% - even in partial load operation (class IE5-IE6)
- Innovative and robust screw compressor stages with new, highly efficient 4+6 profiles
- Extended turndown through the targeted use of VFD technology
- Optimised cooling of the compressor stage and motor thanks to double-walled cooling jackets in both units. Cooling and lubrication are realised by a common oil circuit for both the compressor and the motor
- The PM motor has a high efficiency even at low speeds. The requested quantity of compressed air is adjusted as required by means of a VFD. The harmonised combination of the high-quality drive train and the highly efficient compressor stage results in particularly efficient operation of the entire system
- The rotor of the PM motor is connected directly to the compressor shaft so that additional losses in the drive train are avoided
High reliability and durability
- The compact design of the compressor stage and drive train, which nevertheless allows ideal accessibility, simplifies the maintenance of this unit. The PM motor does not require any anti-friction bearings at all and is therefore characterised by a particularly high level of service-friendliness
- Extended fields of application: option for secure use at particularly high or low ambient temperatures, through to use in extreme external conditions, such as installation in polar regions or in desert areas
- Increased bearing service life of up to 30,000 hours for compressor stages
- The permanent monitoring of the pressure and operating temperatures enables very reliable operation of the entire system
- The oil cooler included in the standard scope of supply sustainably increases the reliability of the package in extreme climatic conditions
Reduced maintenance effort
- Operation and maintenance exclusively from the operating and rear side
- PM motor technology eliminates the need for anti-friction bearing lubrication and bearing changes
- Easy transport of the entire, compact package selectively with pallet truck, fork lift truck or craneWhen delivered, the machine is already filled with oil; therefore, the machine does not need to be filled with oil as part of the commissioning process
Smart oil system
- Only one oil circuit is required for lubrication and cooling of the compressor and motor.
- The integrated oil pressure lubrication of the bearings enables bearing service lives of up to 30,000 hours
Intelligently reduced sound levels
- Minimum sound pressure levels of 70 dB(A) are achieved
- Depending on your requirements, you can choose between different options for sound insulation materials, silencer technologies and acoustic hood designs
- High-quality intake regulator for the reduction of intake losses and noise
- Sound technically optimised acoustic hood
- Thanks to the oil cooling jacket for the PM motor and the use of a centrifugal fan, the lowest noise levels are realised
Compressed air screw compressor SI series - oil-injected, PM Motor
The oil-injected compressed air packages in the SI series with innovative screw compressor stages and highly efficient IE5 class permanent magnet motors. Maximum energy efficiency in full and partial load operation, with differential pressures between 5.5 and 13 bar and drive power from 7.5 - 75 kW.
Oil-injected single-stage Screw Compressor
Series SI
—
Performances & dimensions
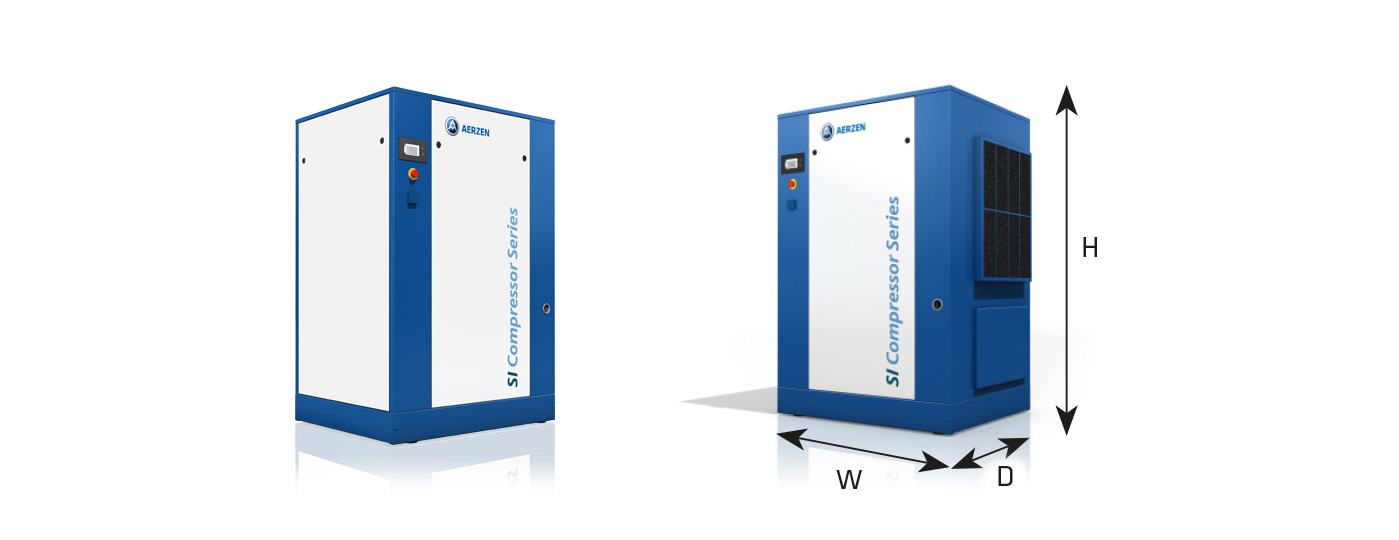
Series | Performance data | Dimensions and weights | |||||
---|---|---|---|---|---|---|---|
Pressure difference, mbar | Volume flow*, m3/h | Motor power, kw | Width (W), mm | Depth (D), mm | Height (H), mm | Weight, kg | |
SI 8 A/W** | 8 bar | 8,000 | 63 | 8 | 660 | 875 | 1,250 | 215 |
SI 8 A/W** | 10 bar | 10,000 | 52 | 8 | 660 | 875 | 1,250 | 215 |
SI 8 A/W** | 13 bar | 13,000 | 42 | 8 | 660 | 875 | 1,250 | 215 |
SI 11 A/W** | 8 bar | 8,000 | 89 | 11 | 660 | 875 | 1,250 | 220 |
SI 11 A/W** | 10 bar | 10,000 | 76 | 11 | 660 | 875 | 1,250 | 220 |
SI 11 A/W** | 13 bar | 13,000 | 67 | 11 | 660 | 875 | 1,250 | 220 |
SI 15 A/W** | 8 bar | 8,000 | 142 | 15 | 660 | 875 | 1,250 | 250 |
SI 15 A/W** | 10 bar | 10,000 | 116 | 15 | 660 | 875 | 1,250 | 250 |
SI 15 A/W** | 13 bar | 13,000 | 98 | 15 | 660 | 875 | 1,250 | 250 |
SI 19 A/W** | 8 bar | 8,000 | 175 | 19 | 770 | 850 | 1,450 | 300 |
SI 19 A/W** | 10 bar | 10,000 | 150 | 19 | 770 | 850 | 1,450 | 300 |
SI 19 A/W** | 13 bar | 13,000 | 117 | 19 | 770 | 850 | 1,450 | 300 |
SI 22 A/W** | 8 bar | 8,000 | 216 | 22 | 770 | 870 | 1,450 | 320 |
SI 22 A/W** | 10 bar | 10,000 | 183 | 22 | 770 | 870 | 1,450 | 320 |
SI 22 A/W** | 13 bar | 13,000 | 157 | 22 | 770 | 870 | 1,450 | 320 |
SI 30 A/W** | 8 bar | 8,000 | 281 | 30 | 850 | 980 | 1,750 | 470 |
SI 30 A/W** | 10 bar | 10,000 | 252 | 30 | 850 | 980 | 1,750 | 470 |
SI 30 A/W** | 13 bar | 13,000 | 220 | 30 | 850 | 980 | 1,750 | 470 |
SI 37 A/W** | 8 bar | 8,000 | 370 | 37 | 850 | 980 | 1,750 | 540 |
SI 37 A/W** | 10 bar | 10,000 | 320 | 37 | 850 | 980 | 1,750 | 540 |
SI 37 A/W** | 13 bar | 13,000 | 275 | 37 | 850 | 980 | 1,750 | 540 |
SI 45 A/W** | 8 bar | 8,000 | 443 | 45 | 950 | 1,180 | 1,750 | 660 |
SI 45 A/W** | 10 bar | 10,000 | 386 | 45 | 950 | 1,180 | 1,750 | 660 |
SI 45 A/W** | 13 bar | 13,000 | 332 | 45 | 950 | 1,180 | 1,750 | 660 |
SI 55 A/W** | 8 bar | 8,000 | 562 | 55 | 950 | 1,180 | 1,750 | 790 |
SI 55 A/W** | 10 bar | 10,000 | 505 | 55 | 950 | 1,180 | 1,750 | 790 |
SI 55 A/W** | 13 bar | 13,000 | 426 | 55 | 950 | 1,180 | 1,750 | 790 |
SI 75 A/W** | 8 bar | 8,000 | 726 | 75 | 1,330 | 2,300 | 1,670 | 1,600 |
SI 75 A/W** | 10 bar | 10,000 | 672 | 75 | 1,330 | 2,300 | 1,670 | 1,600 |
SI 75 A/W** | 13 bar | 13,000 | 548 | 75 | 1,330 | 2,300 | 1,670 | 1,600 |
Sound pressure level without blow-off noise, with acoustic enclosure.
* corresponds to the measured delivery volume flow converted to the customer-specific suction conditions p = 1,0 bar, t =20°C, rF = 0%
**Cooling: A: air-cooled and W: water-cooled