Holzkirchen
With AERsmart made by AERZEN Holzkirchen wastewater treatment plant saves about 50,000 kWh every year
Holzkirchen wastewater treatment plant has a clearly formulated job: “We purify our wastewater optimally.” With its wastewater treatment plant designed for a population equivalent of 50,000, the municipal enterprise, located 40 kilometres south of Munich, not only pursues this target, but also the claim to act as resource-saving as possible. Together with AERZEN they commissioned a blower technology, which, from an energy efficiency perspective, sets a new milestone for the entire industry.
Partial load reduces the efficiency, impairs the energy efficiency and thus increases the operational costs. This context applies for all industries and has a serious effect in wastewater treatment plants mainly in the biology. The electrical energy for the drive of the blowers causes about 80 per cent of the costs in this field of sewage water cleaning. Consequently, efficiency increases and a really tailor-made design of the blowers to the daily requirement pay off accordingly fast. The question remains how the changing air requirement in the aeration basins can be covered optimally and not at the expense of overdimensionings and inefficient partial load.
Beyond cascading
Every blower only reaches its optimal operating point in a clearly defined performance range and works then with maximum efficiency. The air consumption in the biology is subject to considerable variations. The performance cascading with packaged units in a row as well as the variable speed control of the blower drives are important approaches to supply the aeration basins needs-oriented with oxygen. With the new AERsmart control system AERZEN takes another step.
By co-ordinating in partial load operation different blower types with each other on the basis of the required air volume, the new AERsmart solution avoids partial load of individual packaged units to a large extent. Comparable with an autopilot, AERsmart takes over the complete control- and regulating management of a compressor group of up to twelve machines. The new solution goes beyond a simple cascaded connecting or shutdown. The sense of this technology rather is grouping blower units with different operating principles. Messrs. “Gemeindliche Einrichtungen und Abwasser Holzkirchen -GEA” (Municipal facilities and wastewater Holzkirchen), for example, covers the base load requirements with an AERZEN turbo compressor. With a motor rating of 60 kW, type TB75-0.8S supplies an oil-free volume flow of 2,900 cubic metres per hour with a differential pressure of 0.8 bar. As the term base load says the turbo compressor serves for covering the medium requirement. In case of peak loads the machine is not sufficient and with low loads the unit loses considerably in efficiency.
In Holzkirchen, this context leads to the fact that Messrs. GEA combines the turbo compressor with an AERZEN rotary lobe compressor series Delta Hybrid as well as two Delta Blowers with older manufacture dates. These were already available before the modification and now mainly serve as redundancy for operational reliability. AERsmart ensures that the Delta Hybrid starts with the air supply of the aeration basins, when the oxygen consumption at low load reaches a level where a turbo would be underchallenged and leaves its optimal operational range. In reverse direction Delta Hybrid and Delta Blower help out in case of peak loads. This can occur “particularly on hot summer days, when the oxygen consumption is high,” explains plant manager Markus Spallek.
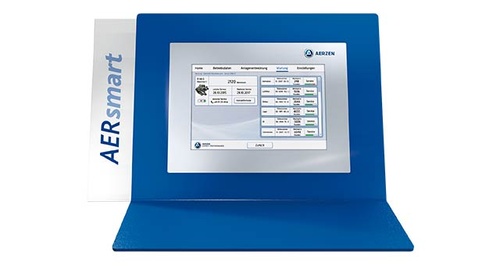
Savings of € 10,000.-- every year
In Holzkirchen, AERsmart has been running excellently from the beginning - which reflects in perceptible energy savings of about ten per cent. What the final rate of the saving potential will be mainly depends on how good the plant worked before. “We had already optimised our processes. Therefore, for us, ten per cent is much.” Expressed in figures: In Holzkirchen, every year about 500,000 kWh of electrical energy are spent for the aeration basins. So, the savings of 50,000 kW protect the city’s purse noticeably - by reduced expenditure of EUR 10,000.--. With this, the solution installed consisting of turbo blower and AERsmart will have paid off after about three years.
AERsmart acts as autopilot
In normal operation the turbo blower runs in “optimal operating point” - which you can see on the AERsmart display with the pointer in the green sector. Looking on the visualisation of AERsmart you can see a conveying volume of 34 cubic metres per minute. If the requirement is between 28 and 16 cubic metres the Delta Hybrid is used. “Starting from 24 cubic metres AERsmart switches the Turbo off,” reports Spallek. According to the plant manager’s experiences the required air volumes are only a part of the design features, as also the necessary blow-in pressures are important for the decision which technology is the most effective one. “If the basins are flatter and consequently the pressure is lower, a positive displacement blower can be an efficient solution.”
With all the technical innovations and a general “We have always paid attention to energy efficiency”, in Holzkirchen first of all the focus is on the water quality. “Our premise is to purify wastewater optimally. And this at a price which is as cost-effective as possible. This approach deviates from the industry. But plants want to purify their wastewater as cost-effective and as good as necessary.” The point that in the southern suburbs efficiency is so important results from the fact that the economical use of resources is one of Andreas Spallek’s hobbies. The plant counts “on reasonable solutions, which increase the efficiency and not on technical gadgets.” It is clear to the expert that water can only be purified reliably by means of a certain energy input. “With a good machinery pool we can reach our goal of generating the required air volume economically.” Consequently, the plants are optimised permanently and the use of energy is improved.
Wastewater treatment plants as energy centres of tomorrow?
This trend will come, to combine different blower types so, that the overall interaction finally generates the required air volumes with an optimal efficiency and maximum energy efficiency,” Spallek is convinced. In his opinion, wastewater plants only have two chances for improving their sustainability: To reduce the energy consumption by using intelligent technology and to increase the self-energy production. Therefore, Holzkirchen also utilises a block-type thermal power station to convert the sewage gas generated in the digestion tower into electricity and to utilise the heat for heating the bioreactor. Another possible solution for Spallek: Decentralised sewage sludge incineration within a local heat network. “Dry sewage sludge has a similar calorific value to lignite.” As in the disposal industry the task in future will increasingly be to recover phosphate from the residues such solutions would be predestined. Wastewater treatment plants as decentral energy centres of tomorrow - and suitable for meeting baseload requirements also when generating electricity?