Screw Compressors
Oil-free double-stage Screw Compressor
Series DS
The double-stage air compressors of the DS series compress absolutely oil-free in accordance with ISO 8573-1, class 0 and guarantee outstanding performance in almost all application areas at differential pressures between 5.5 and 10.5 bar. A compact plug-and-play solution for your processes - not just for sensitive scopes of application.
Volume flow:
180
to
2.920
m3/h
Differential pressure (Δp):
5.500
to
10.500
mbar
Medium:
Air,
Neutral Gases
Compression:
Oil-free
The advantages of AERZEN Screw Compressor Series DS at a glance:
- Increased energy efficiency ensures additional savings of up to 12%
- Large volume flow control range thanks to reliable VFD technology
- Compact design leads to a very small footprint
- Maximum reliability and durability
- Safe use in extreme ambient conditions
- Plug & Play also in connection with outdoor installation and efficient IE5 motors
- Minimum sound pressure levels
- Reduced service costs thanks to extended maintenance intervals
- On-site service on compressor stages and on the package
As diverse as your applications
Compressed air is omnipresent in industry and has become indispensable in many applications - be it in chemical/ petrochemical process technology, electronics and semiconductor production, the food and beverage industry, the textile industry, medical technology and many other areas.
US Units
No- Type of technology
- Screw Compressors
- Design
- Positive pressure
- Differential pressure (Δp)
- 5.500 to 10.500 mbar
- Volume flow
- 180 to 2.920 m3/h
- Medium
- Air, Neutral Gases
- Compression
- Oil-free
Exceptionally high energy efficiency
- Energy savings of up to 12 % compared to other compressor models
- Innovative bare-shaft compressors with new, highly efficient 4+6 rotor profiles in the low and high-pressure ranges
- Large turndown due to the use of VFD technology
- Optimised cooling by using cooling liquid (water or oil) in the double-walled bare-shaft stages
- Motors of energy efficiency class IE4 or IE5; in connection with an integrated VFD
- Direct drive by means of coupling and gear transmission for optimum drive efficiency
- Stainless steel rotors in both stages to prevent corrosion
High reliability and durability
- 100 % oil-free process air for sensitive applications, certified according to ISO 8573-1 Class 0
- PFAS-free process air generation
- Effective sealing concept for drive shaft and conveying chamber; minimisation of natural seal wear
- Extended fields of application: options for using the package in hot, dusty (desert installation) or extremely cold (polar regions) climates.
- Oil pressure lubrication for exceptional durability of the anti-friction bearings. Bearing life of up to 40,000 hours
- Permanent oil level check by means of an electrical oil pressure switch
- Reliable even in extreme climatic conditions thanks to the use of an oil cooler already included in the standard scope of supply
- Optional acoustic hood for outdoor installation. Enables the machine with integrated VFD to be used outdoors even under direct weather conditions
- Highly effective water separators ensure that condensate is drained as required
Reduced maintenance effort
- Operation and maintenance exclusively from the operating and rear side of the package
- Small footprint and side-by-side installation possible
- On-site service on the compressor stages and the package
- Effortless transport of the entire package using a pallet truck, fork lift truck or crane
- No maintenance required for drivetrain components
- Delivery of the package with a filled oil system enables quick commissioning
Smart oil system
- Mechanically driven oil pump on the drive shaft
- Highly efficient oil pump with reduced energy consumption
- Oil-lubricated anti-friction bearings with pressure lubrication achieve a service life of up to 40,000 hours
Permanently, intelligently reduced noise levels
- Minimum sound pressure levels thanks to intelligent noise reduction of the package
- Innovative pulsation reduction thanks to the use of Venturi nozzles downstream of both compressor stages
Compressed air screw compressor DS series - double-stage, oil-free
The double-stage air compressors in the DS series compress absolutely oil-free in accordance with ISO 8573-1, class 0. Outstanding performance in almost all application areas with differential pressures between 5,5 and 10.5 bar. Compact plug-andplay solution for drive power from 55 - 315 kW.
Oil-free double-stage Screw Compressor
Series DS
—
Performances & dimensions
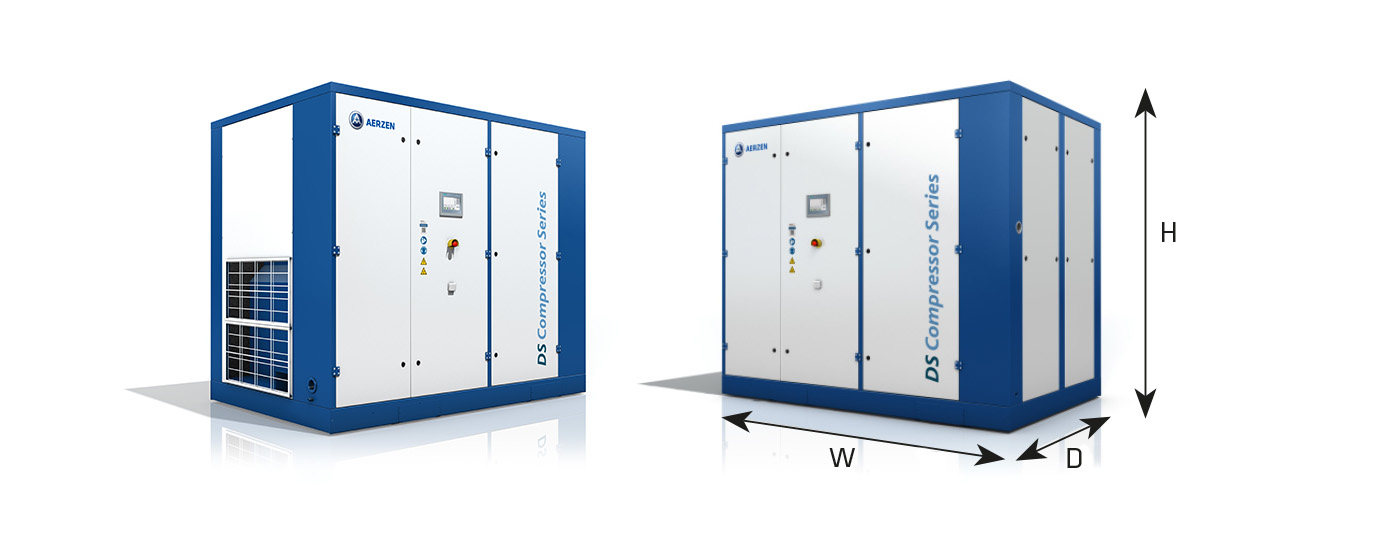
Series | Performance data | Dimensions and weights | |||||
---|---|---|---|---|---|---|---|
Pressure difference, mbar | Volume flow*, m3/h | Motor power, kw | Width (W), mm | Depth (D), mm | Height (H), mm | Weight, kg | |
DS 55 A/W** | 8 bar | 8,000 | 475 | 55 | 1,400 | 2,500 | 2,000 | 3,060 |
DS 55 A/W** | 10 bar | 10,000 | 397 | 55 | 1,400 | 2,500 | 2,000 | 3,060 |
DS 75 A/W** | 8 bar | 8,000 | 719 | 75 | 1,600 | 2,800 | 2,000 | 3,270 |
DS 75 A/W** | 10 bar | 10,000 | 587 | 75 | 1,600 | 2,800 | 2,000 | 3,270 |
DS 90 A/W** | 8 bar | 8,000 | 804 | 90 | 2,200 | 2,800 | 2,000 | 3,370 |
DS 90 A/W** | 10 bar | 10,000 | 648 | 90 | 2,200 | 2,800 | 2,000 | 3,370 |
DS 110 A/W** | 8 bar | 8,000 | 1,079 | 110 | 2,200 | 3,300 | 2,000 | 4,080 |
DS 110 A/W** | 10 bar | 10,000 | 943 | 110 | 2,200 | 3,300 | 2,000 | 4,080 |
DS 132 A/W** | 8 bar | 8,000 | 1,273 | 132 | 2,100 | 3,400 | 2,400 | 4,680 |
DS 132 A/W** | 10 bar | 10,000 | 1,143 | 132 | 2,100 | 3,400 | 2,400 | 4,680 |
DS 160 A/W** | 8 bar | 8,000 | 1,542 | 160 | 2,200 | 4,000 | 2,200 | 5,000 |
DS 160 A/W** | 10 bar | 10,000 | 1,350 | 160 | 2,200 | 4,000 | 2,200 | 5,000 |
DS 200 A/W** | 8 bar | 8,000 | 2,056 | 200 | 2,000 | 4,000 | 2,600 | 5,200 |
DS 200 A/W** | 10 bar | 10,000 | 1,714 | 200 | 2,000 | 4,000 | 2,600 | 5,200 |
DS 250 A/W** | 8 bar | 8,000 | 2,447 | 250 | 2,000 | 4,000 | 2,600 | 5,450 |
DS 250 A/W** | 10 bar | 10,000 | 2,195 | 250 | 2,000 | 4,000 | 2,600 | 5,450 |
DS 315 A/W** | 8 bar | 8,000 | 2,920 | 315 | 2,000 | 4,000 | 2,600 | 5,650 |
DS 315 A/W** | 10 bar | 10,000 | 2,663 | 315 | 2,000 | 4,000 | 2,600 | 5,650 |
Sound pressure level without blow-off noise, with acoustic enclosure.
* corresponds to the measured delivery volume flow converted to the customer-specific suction conditions p = 1,0 bar, t =20°C, rF = 0%
**Cooling: A: air-cooled and W: water-cooled