Performance³
Aeration of wastewater treatment plants according to demand
The economic efficiency of modern wastewater treatment plants is significantly influenced by the energy consumption of the various process steps during wastewater treatment. The energy-intensive process of biological aeration is a particular focus of attention in this regard: around 60 to 80 percent of the total energy requirement is generated here. At the same time, wastewater tank aeration offers great energy-saving potential that can be exploited by operators of wastewater treatment tanks.
As an experienced specialist for water and wastewater technology, AERZEN has always set new standards for energy efficiency in aeration tanks. The innovative Performance³ concept is the most efficient, powerful and flexible technology solution for demand-driven oxygen supply in wastewater treatment tanks. The unique selling point of Performance³ is its optimised adaptation of blower output to individual load fluctuations and different degrees of contamination. But which technology powers Performance³? How do the different blower technologies interact in the aeration tank and how can different power requirements and volume flow ranges be combined in a technically sensible way?
In simplified terms, Performance³ refers to the approach of configuring machine technologies to a plant's individual requirements in order to achieve the most efficient aeration solution. The aim is to optimally meet the fluctuating load requirements and, taking into account the available technologies, to always operate with the most efficient machine usage.
Three different blower technologies are suitable for this: positive displacement blowers, rotary lobe compressors and turbo blowers. Depending on the system configuration and capacity usage, these technologies can be switched in a way that achieves maximum efficiency through their strengths in interaction or as individual solutions. Efficiency values can be further improved in conjunction with the AERsmart global control system, which ensures optimum distribution of air volumes to each assembly.
Performance³ - what is it all about?
For every system configuration, Performance³ enables you to find exactly the right blower solution that represents the optimum from a technical and economic point of view. While it used to be common practice to install blowers of just one size, today’s plants often feature a mix of different sizes or even technologies. Savings of up to 30% are possible. To fully understand the far-reaching benefits of Performance³, a certain understanding how blower technologies are applied in wastewater treatment tanks is required.
Performance³ in your wastewater treatment tank
The main challenge when aerating wastewater treatment tanks is in meeting the constant fluctuations in the load profile at all times. An aeration tank's air requirement is influenced by a number of different factors. Depending on the region, time of day and amount of precipitation, different degrees of pollution and strong fluctuations occur within the load curves.
For a long time, the fluctuating load profile in the wastewater treatment tank was countered with a stand-alone blower that covered the entire load profile. The consequence was that, due to the fluctuating demand profile, the blower seldom runs at the optimum operating point; this is also accompanied by inadequate energy efficiency and unnecessarily high energy consumption. The choice of aeration solution can severely impair the profitability of an entire wastewater treatment plant. This is exactly where Perfomance³ comes in: By enabling the interaction of different technologies, sizes and design points, we implement individual blower solutions that allow energy savings of up to 30%. With many wastewater treatment tanks, investment in the efficiency measure pays for itself faster than expected; depending on the plant, the payback period is only around two years.
Blower technologies in focus
In order to match the choice of blower technologies precisely to the individual load curves in the wastewater treatment plant in question, a thorough understanding of the areas of application of the various technologies is required.
In the following, we thus provide an overview of the three blowers' technical characteristics.
How three technologies become one intelligent solution
Three innovative and technically sophisticated technologies alone do not make a tailor-made blower solution. In addition, precise measurement and evaluation of real operating data as well as an intelligent, higher-level control system are required for process and energy-efficient clarification operation. This is the only way to optimally allocate the volume flow required by an aeration tank to the used technologies at all times and to find the optimum degree of efficiency. AERZEN has developed the two solutions for this purpose: AERaudit and AERsmart.
The volume requirement determination lays the foundation for efficient and sustainable operation of your wastewater treatment tank. For this reason, we carry out an on-site measurement as a first step and record all relevant data of your aeration system with a mobile measuring station. Whether it be volume flow, pressure, temperature or power – all operating data is recorded in the form of load curves.
During the subsequent analysis, our specialists evaluate the collected data and develop a tailor-made concept based on the results. The focus here is always on efficiency: Taking into account the real load curves and requirements, a conclusive operating concept is drawn up, which reduces the energy requirement to a minimum through the use of the appropriate blower technologies, each with optimum workload.
In a transparent report, we visualise the most important results of the volume requirement determination for you. This not only allows us to show you the ideal machine configuration, it also allows us to calculate the savings potential and the payback period of the modernisation measure in no time at all.
Even the best system won't achieve the requested results without an intelligent, higher-level control system – that's why we use the AERsmart global control system. It certainly lives up to its name and ensures that the required air volumes are distributed exactly in accordance with the blower characteristics. By considering the individual efficiencies, it is possible to achieve first-class efficiency values and to always have the blower operating at the best possible operating point.
Even if strong and abrupt load changes occur in the aeration tank, the machine control system gets the job done and intelligently distributes the oxygen demand in the shortest possible time. This means that third-party equipment and installations can also be operated with just one machine technology.
Performance³ in practice – the Rheda-Wiedenbrück Wastewater Treatment Plant
The aeration system in the Rheda-Wiedenbrück Wastewater Treatment Plant was operated for years with an old positive displacement blower, so it was high time for modernisation. AERZEN installed a tailor-made combination of turbo blower and rotary lobe compressor Delta Hybrid, which has already resulted in a savings potential of 30 percent. Based on the Performance³ configuration, the AERsmart integrated control system was then able to fully exploit its strengths and reduce the system's energy consumption by a further eight percent.
Today, the wastewater treatment plant still supplies a population equivalent of around 326,000 in the Rheda-Wiedenbrück area in addition to Germany's largest slaughterhouse. Thanks to the tailor-made Performance³ solution, energy costs were reduced by around 40,000 Euro per year.
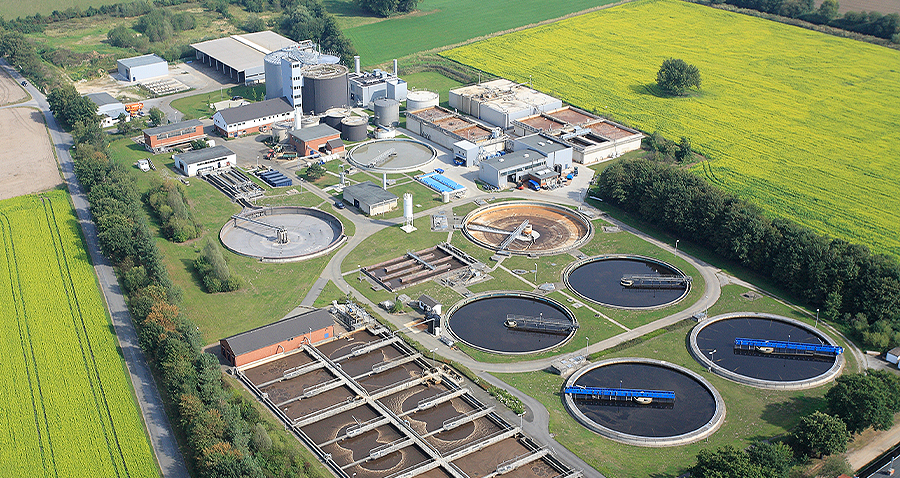
Performance³ for your wastewater treatment plant – we will be pleased to advise you
The energetic optimisation of wastewater treatment plants requires not only the right technology, but also and above all technical expertise. It is only when the advantages of the blower technologies can be tailored to the individual requirements that the optimum result can be achieved.
For this reason, the experienced specialists at AERZEN take care of the complete project management; from the first inventory on site, to the execution and evaluation of measurements and the design of the plant concept, all the way to the implementation of the measure.