The digital twin doesn’t yet play a significant role in the wastewater sector, but the potential in terms of process optimisation is enormous. As the most advanced wastewater treatment plant in Europe, the new Upper Engadine WWTP in Switzerland has dared to take a step into the future and show how water protection and cost efficiency can be optimally harmonised with state-of-the-art technologies and a sustainable energy concept. On board: highly efficient rotary lobe compressors resp. screw blowers from AERZEN.
- Article The most modern wastewater treatment plant in Europe
Upper Engadine WWTP (Switzerland): maximum efficiency in activation thanks to AERZEN rotary lobe compressors

The wastewater treatment plant of the future is energy-efficient, re-source-saving, compact and economical. What this looks like in practice is on show in Switzerland - more precisely at the high valley of Oberengadin (Canton Graubünden). In the small village of Schanf on the upper reaches of the River Inn - a good 20 km. north-east of St. Moritz - one of the most modern and innovative wastewater treatment plants in Europe went into operation in July 2021. The Upper Engadine WWTP was planned and realised according to the latest state-of-the-art - keyword digital twin - and im-pressively proves that ecology and economy are not opposites. “While sustainability is a key focus, economic efficiency is just as important,” is how Plant Manager Godi Blaser sums it up. The result is a quantum leap for the region and a blueprint for wastewater treatment in the future.
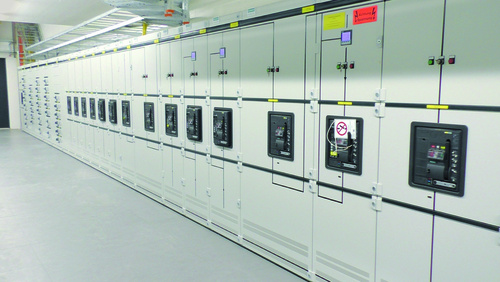
Combination of three wastewater treatment plants
The starting point for the new construction was insufficient nitrification in the Upper Engadine wastewater treatment plants Staz in Celerina, Sax in Bever and Furnatsch in Schanf, which meant that the water protection requirements could no longer be met. The question was: should the three plants, which were variously built in the 1970s and 1980s, be renovated or should their capacities be combined in a new regional wastewater treatment plant for Upper Engadine?
Although the investment costs of 74.6 million Euro for a new plant were higher than for an expansion of the three existing WWTPs (50,7 million Euro), the envisaged operating costs were significantly lower - 1.8 million versus 2.5 million Euro per year. Assuming 45 years of operation, this results in significant savings.
The new Upper Engadine WWTP was built on the site of the old Furnatsch WWTP and is designed for 90,000 population equivalents (PE). This makes it considerably smaller than the Staz, Sax and Furnatsch WWTPs, which have a total capacity of 114,000 PE. This was made possible by the main collection channel from Samedan to S-chanf, which was already built in 2009, a consistent separation of meteoric water (rain, meltwater) from polluted wastewater, and optimised process engineering during the peak tourist season around Christmas and New Year. The plant has a modular structure. This means that the Upper Engadine WWTP is also optimally equipped to cope with wide seasonal fluctuations: while peak loads of up to 110,000 PE occur in the peak season, the pollution load in the low season corresponds to just 15,000 PE.
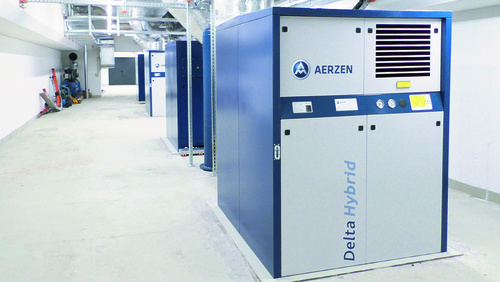
Life cycle costs as a determining factor
When choosing the technologies, solutions and materials to be used, the focus was primarily on life-cycle costs. This means that it was not only the procurement costs that counted, but also the operating costs, i.e. expenses for electricity, maintenance, personnel, etc. For the SBR biology (SBR = Sequencing Batch Reactor), the heart of the plant, this meant that energy efficien-cy and availability in service were largely the decisive factors. Particular attention was paid to the aeration system, as this can consume between 60 and 80 per cent of the total energy required for wastewater treatment.In the Upper Engadine WWTP, AERZEN rotary lobe compressors of the type Delta Hybrid D 52S with a maximum intake vol-ume of 40.9 m³/min, a pressure difference of 650 mbar and a volume flow control range of more than 1:4 ensure optimum oxygen supply to the five SBR reactors - one Delta Hybrid per basin (basin volume 2,700 m³). An additional compressor would normally be required as redundancy. How-ever, thanks to the high reliability of the AERZEN packages, and the fact that all SBR reactors are rarely in operation at the same time due to seasonal fluctuations, the Upper Engadine wastewater treatment plant deliberately decided against this.
Condition monitoring of the blowers
The Upper Engadine WWTP wanted to cover all processes with the same type of converter on site and commissioned an extra partner for this purpose. Therefore, packages without frequency converters were required. No problem for AERZEN. The blower and compressor specialist offers a great deal of flexibility here and can supply its equipment with integrated, separate, or, as in the present application, without a converter. The frequency converters also monitor the condition of the blowers. Speed or frequency allow conclusions to be drawn about the current volume flow and thus the actual load. In the future, predictive maintenance will also be targeted, because as the largest energy consumers, the blowers are particularly predestined for needs-based maintenance. “I am glad that we are working with AERZEN blower technology. With AERZEN, we have a partner who not only supplies reliable and efficient technology with minimal maintenance, but also offers excellent service. Whenever there is something wrong, we can always rely on AERZEN to be there within a very short time,” says Godi Blaser enthusiastically. In addition, two robust positive displacement blowers of the Delta Blower type are being used in the grit chamber.
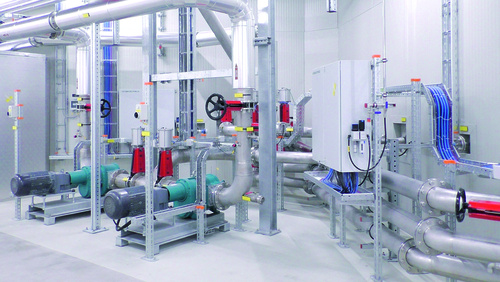
A special feature is the installation altitude of 1,650 metres above sea level. Due to the lower air pressure and the resulting lower air density, a higher volume flow is needed to get enough oxygen molecules into the aeration. Also, the pressure ratio is higher (in this case it can vary between 1.5 and 2) and a motor derating has to be taken into account. As a result, more powerful packages are needed at altitude than at sea level. Against this background, the issue of energy efficiency becomes even more relevant. The highly efficient Delta Hybrid D 52S are exactly the right choice, because thanks to their technological superiority they enable significant energy savings of up to 30 percent compared to classic blower technology.
The entire process management of the Upper Engadine WWTP is highly automated via a powerful control system and enables the operating staff to carry out the necessary monitoring, data evaluation and process optimisation. The control of the SBR reactors is implemented dynamically. The SBR process is a variant of the activated sludge process. In contrast to the conventional method, in which all purification steps take place one after the other in different basins, the SBR process combines biological purification and secondary sedimentation in one reactor. This results in a particularly high degree of flexibility.
Pioneer in digital twin
“It is important to us that the systems run reliably and that we have no failures. Due to the dynamic control, the system is so complex in itself that you can’t necessarily see the effects of a measure immediately. That’s why we rely on the digital twin. This gives us the possibility to simulate operating scenarios in advance,” Godi Blaser explains. In the simulation model, strategies and variants can be examined and forecasts and options for action can be shown. The results then flow into the dynamic control system.
State-of-the-art technology combined with a sustainable energy concept: history has been made in the Upper Engadine. The digital twin is a novelty in Europe’s wastewater management - and already so successful that imitators will certainly not be long in coming. Godi Blaser emphasises: “The aim of the digital twin is not to take over control. The digital twin is a tool and if you see it as such, it is very valuable.
”As soon as all processes are running smoothly, an annual electricity demand of 1.4 GWh is estimated for the Upper Engadine WWTP, of which 1.2 GWh will be generated from pure WWTP operation. The goal: 80% energy self-sufficiency. Energyefficient, reliable and low-maintenance technology such as the AERZEN packages make a significant contribution to this. By the way, if you add in external processes such as the solar plant or the biogas production from the whey delivered to the plant, it even goes into overdrive.