With an investment of around one million euros, Stadtwerke Bramsche has fundamentally modernised its wastewater treatment plant. The main focus of the project, which received almost 50 percent public funding, was on upgrading the aeration tanks. The objectives: great cleaning capacity with improved energy efficiency. One of the triggers for this ambitious modernisation project was the expansion of production at a large food processing plant in Bramsche.
- Article Now the air comes from the ground
Energy demand reduced by more than 50 percent: Bramsche wastewater treatment plant’s new aeration system
Conclusion
The Bramsche wastewater treatment plant shows how today, with available technology and the appropriate control intelligence, the biological degradation processes in wastewater can be supplied with oxygen in an efficient and, above all, energy-saving manner. All in all, we have succeeded in increasing the cleaning capacity with the help of a more intelligent process, while at the same time reducing electricity costs. “Investments were made in optimisations and not in concrete - in other words, the structural expansion of the tanks,” says Markus Leidinger. The savings are significant. The demand for electrical energy fell from just under 140,000 kWh per month to around 60,000 kWh per month. In monetary terms, this represents an amount of over €195,000 per year, assuming a kilowatt hour price of 21 cents.
Optimal room ventilation
The system installed in Bramsche is characterised by coordinated ventilation of the machine building and thus ensures optimal operating conditions for the blowers. Because rising internal temperatures in the machine room also have an effect on efficiency - and thus on power consumption. A 15°C higher room temperature means an energy loss of 5 %. Warm air has a lower density than colder air. Consequently, less oxygen per cubic meter arrives in the aeration. This in turn lengthens the switch-on times and means higher energy costs.
AERsmart takes over the regulation
To ensure that the air rising from the aerator plates at the bottom of the aeration tanks carries sufficient oxygen, AERsmart is in turn connected to the plant control system or the process control system of the Bramsche wastewater treatment plant. The plant continuously measures the ammonium and nitrate values for control purposes. The data flows into an Optec biology controller that takes into account all the interrelated degradation processes. Having this holistic view means that necessary oxygen demand can be calculated, which the AERsmart in turn converts into a volume flow, and determines, according to the efficiency curves, which assembly best covers the demand energetically.
Using heat effectively?
The wastewater company gains further efficiency through heat recovery on the discharge side of the D52 S Hybrid packages. About 40 kW of thermal power can be used today to heat the heating return. “That’s enough for the entire workshop building and is nominally about 80 percent of our total demand,” says Frank Möller, Manager of the wastewater treatment plant. The aim of heat recovery is to use the thermal energy produced during the compression of gases as effectively as possible.
AERsmart: the energy manager
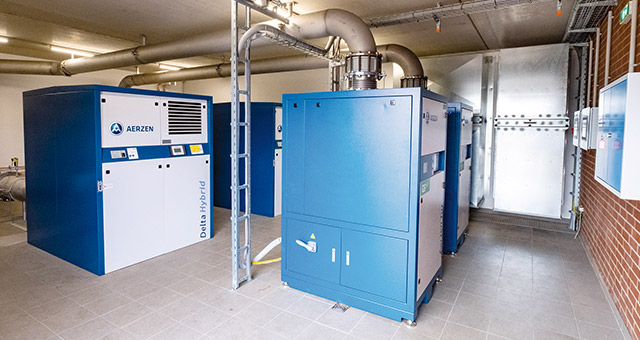
This solution, which involves a hybrid and turbo blower combination, means that electrical energy is handled much more intelligently - and thus more efficiently. This architecture results in energy savings of more than 50 percent at the Bramsche wastewater treatment plant compared to the previous aeration of the two five-meter-deep aeration tanks with surface rotors. Markus Leidiger, Application Manager Wastewater at AERZEN, sees the success of the Bramsche project not only at the hardware level. “The energy savings of more than 50 percent were achieved by all project participants working together. A number like that doesn’t just happen on its own. It involves everyone working well together.” What is also required is control intelligence that regulates the network completely automatically. At Bramsche, AERsmart coordinates the two blower types in a load-optimised manner according to optimum efficiency. As already briefly described, at Bramsche the AERZEN Turbo serves the basic oxygen load - which is the case during most of the nitrification period. In low-load phases, AERsmart intervenes, takes the turbo off the grid and switches at this operating point to the more efficient Delta Hybrid of type D52 S. Both assemblies operate together when the wastewater values require maximum oxygen due to a high load.
Efficiency rates optimally combined
The combination of Aerzen Turbo and Delta Hybrid creates the basis to cover the complete operating range of the wastewater treatment plant according to the load curve with maximum efficiency. The AT150 0.8S turbo serves as the base load machine and covers about 60 to 70 percent of the complete operating time in an energy-efficient manner. In low-load phases, the turbo goes off-line and the oxygen supply of the activation is transferred over to Delta Hybrid D52 S rotary lobe compressor. In the high-load phase with correspondingly abundant COD values, both assemblies are again active.
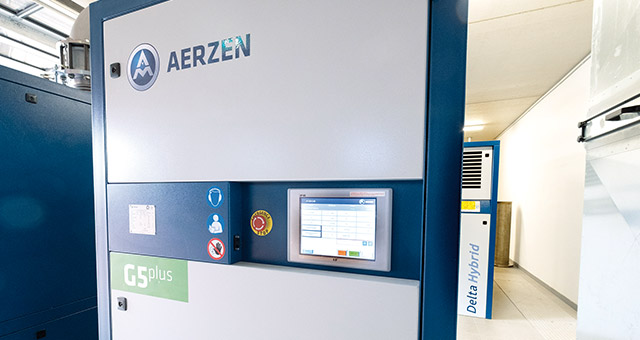
Fifty-fifty or 50 percent municipal, 50 percent industrial: this is how plant manager Frank Möller describes the composition of the wastewater from his wastewater treatment plant, which was built in 1962. The wastewater treatment plant in Bramsche is designed for 60,000 population equivalents (p.e.) and has a current capacity utilisation of 54,000 p.e. After two expansions in 1972 and 1988, fundamental modernisations have been on the to-do list for the past three years. In focus: new aeration technology for the two aeration tanks. They each have a capacity of 4300 cubic meters. Instead of introducing the atmospheric oxygen with surface rotors as before, fine-bubble aerators were planned at the bottom of the five-meter-deep tanks. This measure primarily pursues the twin goals of improving cleaning performance and energy efficiency. A combination of turbo blower and rotary lobe compressor from AERZEN now provides the necessary oxygen input for each tank. The two assemblies work together to supply the aeration system as required - with optimised efficiency and thus maximum energy efficiency.