Aeration openings which have become too narrow, blocked aeration grids, excessive internal temperatures and clogged filter mats are four examples of situations in machine rooms that drive up energy consumption in wastewater treatment plants. They are the main causes of poor efficiency of the compressed air generators which bring the oxygen into the aeration tanks. The good news: all four can be eliminated with little effort and a manageable financial investment.
- Article It‘s the oxygen that counts
Thermodynamics in the machine room: so that the blowers do not run out of air
Effective exhaust air takes out temperature
The exhaust air louver is to be positioned in the machine building, in relation to the supply air louver, “so that we obtain as diagonal a flow machine pattern as possible in the interior,” explains Torsten Lehmann. The main task of the exhaust air louver is to conduct excess heat to the outside. The same applies to the exhaust air as to the supply air in terms of noise emissions: the heat has to go out, the sound stays in. Hence, AERZEN equips exhaust air louvers with silencer elements and uses exhaust air fans to ensure that the warm air leaves the room quickly. Torsten Lehmann: “It makes sense to mount the exhaust fans at ceiling height, where the air is warmest.” Particularly with regard to temperature distribution, it is important that the machine house is positioned appropriately according to the compass direction. “The supply air is ideally in the north, the exhaust air in the south,” according to Torsten Lehmann, who adds: “The pressure lines in the room should also be insulated. This will make the room noticeably cooler.” Another tip: it is not sufficient to blow out clogged filters with compressed air. “Added filters quickly provide pressure resistance of 25 millibars or more.” In the case of a typical wastewater treatment plant with four blowers, each with 37 kW motor power, 6,900 operating hours per year and at 20 cents per kilowatt hour, the clogged intake filter alone would demand five percent more power from the blowers – that’s more than 10,000 euros a year.The warmer the installation room, the less oxygen is required
Inadequately dimensioned supply and exhaust air ducts give further impetus to another efficiency killer: temperature. What is true for air pressure is true in reverse for temperature. The warmer it gets in the machine house, the thinner the air becomes due to the physical gas laws. It follows that the warmer the air, the fewer oxygen molecules there are per cubic metre. This correlation has a major effect on the biology in the aeration, as with increasing temperature less oxygen is produced. However, the O2 index is decisive for the aerobic nitrification process. The inference: here as well, the assembly must perform better or run longer in order to get the required oxygen into the tank. The consequence of this is that the demand for energy increases. For example, a temperature increase of 3 Kelvin reduces efficiency by about one percent. “Machine rooms can quickly become 20 degrees too warm compared with the temperature outside the machine room - and this means losses in efficiency of 7 percent,” explains Torsten Lehmann. Therefore, for example, heat-radiating frequency inverters do not belong in the installation room of aeration blowers at wastewater treatment plants, but should be in a separate installation room for electrical equipment!
Anyone who thinks that they can simply open a door or a window in a machine house to adjust the inside temperature during day-to-day operations has misunderstood the situation. With the goal in mind that a system can only work most effectively if all aspects that affect it are taken into account, AERZEN has developed splitter silencers for the supply and exhaust air. The units initially provide an effective insertion loss of 30 db. The louvers inside are designed to effectively reduce sound and create little flow resistance so that the assemblies in the machine house do not draw negative pressure. The supply air louver is completed by a weather protection grid, which also prevents birds and leaves from getting into the intake duct.
Supply air versus sound
It is completely irrelevant where aeration blowers get their intake air from: it is important that there is enough of it at the right temperature. This statement, which appears simple at first glance, reveals sophisticated cross-correlations and dependencies in practice. If a rotary lobe compressor (screw blower) such as a Delta Hybrid from AERZEN provides air in the aeration tanks, then this is associated with emissions in terms of sound and temperature. If the design of the machine house were to focus solely on making the outer shell as soundproof as possible, the Delta Hybrid could run out of steam. Background: too little outside air flows into the interior because of the sound insulation. This deficiency causes the positive displacement rotary lobe compressors (screw blowers) to create a negative pressure inside the building. This can go so far that doors can no longer be opened. From a process engineering point of view, the decreasing air pressure means that the assemblies have to work harder in order to press the necessary amount of oxygen into the aeration. The machines have to overcome more differential pressure because the negative intake pressure increases the total pressure.
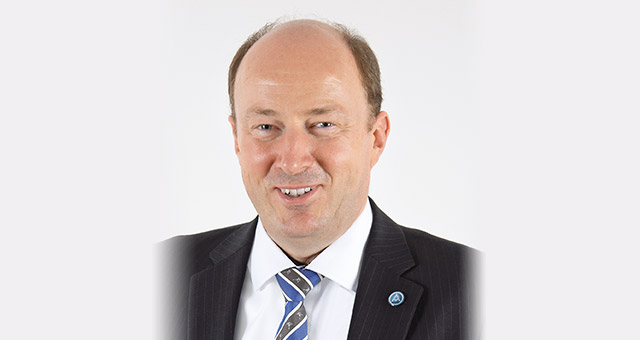
Torsten Lehmann, AERZEN Deutschland, Office Manager North/East
Every reduction in efficiency, even if it’s only by a few percentage points, can add up at the end of the day to a significant loss in overall energy efficiency and this means, higher electricity costs,” says Torsten Lehmann. The Office Manager for Northern and Eastern Germany notes that correct ventilation of machine installation rooms often goes unnoticed at wastewater treatment plants. “After all, aeration of aeration tanks is not directly about the air volume conveyed, but about the necessary amount of oxygen being brought into the wastewater for effective nitrification. This oxygen is exactly what I want to have. It is the most important thing when we talk about blower technology in “compressed air aeration”. Therefore, the industry-standard phrase “compressed air aeration” is actually not correct, as it is not about compressed air but about oxygen input.” The key points in the design are above all a sufficient volume flow, the effective limitation of the temperature in the installation room and also the orientation of the building according to the compass direction. Also, alternative suction of the machines via pipe, i.e. directly from the outside, can bring more disadvantages than advantages, as the intake noise is almost directly shifted to the outside.
Typically 15 percent of energy used is wasted in a poorly designed machine room. The reasons for this are thermal losses due to the heat radiation of the assemblies, mechanical losses due to negative pressure created in the machine installation room and intake losses. But that is by no means the end of the story - particularly if mistakes are made in ventilation.