Through a holistic optimisationprocess, the Aachen-Soers sewage treatment plant has succeeded in reducing the enormous energy requirement of the activation process by around 55 percent. Among other things, rotary lobe compressors with their high energy efficiency over a wide adjustment range replaced the outdated turbo technology. All machines of the AERZEN type Delta Hybrid have also left the familiar environment of central machine rooms and are located under a long roof directly at the basin. Short pipe systems help to keep line losses to a minimum.
- Article Blowers must be arranged close to the basin
Aachen-Soers wastewater treatment plant modernises its activation and decentralises the aeration
Wurm is the name of the river which receives water from the Aachen-Soers sewage treatment plant. And it wasn’t so long ago (in the 20th century to be precise) that this small river on the border with Belgium had heavily polluted water. This came from the wastewater of the coal mines of the former Aachen coal mining area. The Rur tributary (not to be confused with the Ruhr) is just 53 kilometres long. Long sections of this river have either been canalised or straightened. Due to its gravel and sand landings, the Wurm today enjoys a place in nature conservation through small-scale ecosystems in which rare bird species such as the sandpiper and water pipit feel at home.
Nationwide model company
This valuable wildlife habitat came into being because the Wurm lost its sewage-laden character, even though about 80 percent of the water in the river comes from the discharges of sewage treatment plants. And it is precisely this special feature that drives the local residents to top performance when it comes to discharge values into this receiving water. “We use very good engineering within very good processes,” says Thomas Zobel, Head of the Wastewater Treatment Plants Division at Wasserverband Eifel-Rur (WVER) (Eifel-Rur Water Association). The Aachen-Soers sewage treatment plant is part of the WVER supply area and is one of Germany’s leading plants in terms of inlet values, fourth purification stage and energy efficiency.
The Aachen-Soers sewage treatment plant discharges 800 litres per second into the small river, which measures a water flow of just 200 litres per second in front of the receiving water area. With a capacity of 458,000 population equivalents, Aachen-Soers is one of the Class 5 sewage treatment plants which, according to Thomas Zobel, “normally discharge into receiving waters the size of the Rhine.” In this particular case, the quality of the purified water must be correspondingly highend, so that the small river does not get any problem.
The team around Zobel and his wastewater manager Nils Brand have developed an ambition from these general conditions that is setting a precedent nationwide. The ammonium limit, for example, is 0.01 mg per litre. “Other systems with significantly larger receiving waters are used to completely different figures,” says Brand. To ensure that the very good limit values - which for PO4 are 0.1 mg/l - are not at the expense of energy costs, the Aachen-Soers sewage treatment plant has developed an integrated optimisation concept as part of a capacity expansion and has started a two-year large-scale trial for this purpose. The plant offers ideal conditions for this.
Field test on a large scale
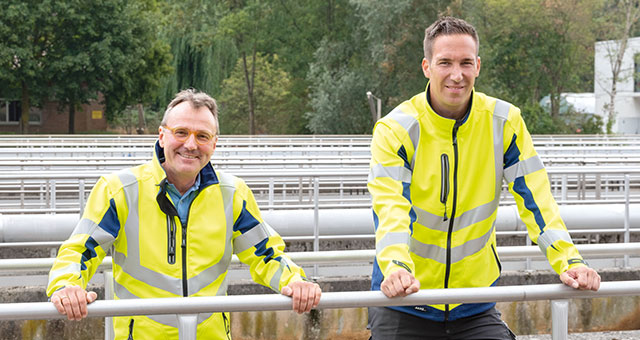
One of the six activation lines available could be used for the field test. After the phase scientifically accompanied by RWTH Aachen University, it was clear that there would be no 1:1 replacement of the ten old turbo blowers of another manufacturer and ceramic fan plates. And the centralised supply of the activation with oxygen out of two machine rooms should belong in the past. “The blowers must be arranged close to the basin to reduce the piping losses,” says Zobel. Furthermore, due to the outdoor installation, optimal inlet conditions for the machines prevail - and consequently very good conditions for the best possible oxygen saturation of the activator basins. This also contributes to increasing energy efficiency, as the running time of the machines is shortened by this efficiency in oxygen supply. In conclusion, the days of the old turbo blowers with guide vane adjustment are over as a result of this innovation. Due to the extremely high maintenance costs, as well as the energetically uneconomical operation in the partial load range, they are no longer up-to-date and have consequently been replaced by modern, speed-controlled rotary lobe compressors of the AERZEN Delta Hybrid series. Today, ten assemblies type D 52 S and seven assemblies type D 36 S with consistently the same motor rating of 55 and 45 kW have been assembled on the central bridge of the six activation lines - strung like a string of pearls. Two Delta Hybrids are directly assigned to each line. All others cover the increased air demand during nitrification and supply two lines at a time.
Speed control instead of throttle valves
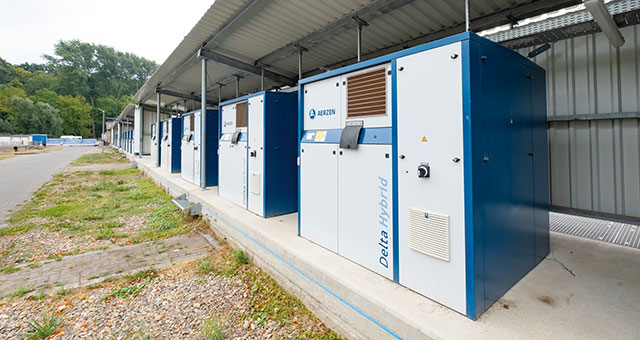
The wide control range of the Delta Hybrid rotary lobe compressors, due to their design, paves the way for the Aachen-Soers wastewater treatment plant to ensure a demand-oriented supply of oxygen to the activator basins without throttle valves or slide valves. Whereas in the past a sliding pressure control was derived from the oxygen content, “today we regulate according to the nitrogen content,” explains Brand. Ammonium and nitrate concentrations play just as important a role as the amount of waste water and the oxygen content. “Roughly speaking, we dose the air for each line individually according to the ammonium load,” explains Zobel. This supply, which was optimally adapted to the prevailing process conditions in the individual lines, was not possible with a central infrastructure and volume distribution with throttles and slide valves.
The finer adjustment options improve the cleaning performance of the system on the one hand and noticeably increase energy efficiency on the other. After optimisation, the electrical connected load of the entire sewage treatment plant fell by almost one third from 1,100,000 kWh in 2016. If the focus is on the pure process area of biology, the increase in efficiency through the new ventilation concept is even more pronounced: 320,000 kWh today compared with 720,000 kWh before - which corresponds to a reduction in consumption of 55 percent.
No minimum ventilation volume is necessary
These long-term energy savings are also the result of new polyurethane (PUR) plate aerators. “These are much easier to control and can also be taken completely off the grid,” says wastewater master Brand, looking at the old ceramic units. They had to be continuously ventilated so that they did not clog - which resulted in correspondingly high energy costs for standby operation. As no minimum ventilation volume is necessary now, the complete adjustment range of the Delta Hybrid rotary lobe compressors from AERZEN can be used for control without regard to standby questions. In contrast with the old turbo blowers with guide vane adjustment, which quickly and massively lose efficiency to the right and left of the nominal operating range, the Delta Hybrids operate efficiently over a wide speed setting range.
Résumé
Energy savings are becoming more and more important in sewage water cleaning. Municipalities and associations are increasingly focussing on themoney element. This was certainly the case at Aachen-Soers. However, there is agreement that efficiency improvements must not be at the expense of cleaning performance. On the other hand, sewage treatment plants that are about to be modernised due to their age offer plenty of potential for achieving better values more economically. The intelligent supply of oxygen to the activator basins plays a key role here in conjunction with holistic process improvements. Based on this modification, the Aachen-Soers wastewater treatment plant became an international reference plant for the German Water Partnership, a renowned network of the German wastewater industry, which enables foreign operators and engineering offices to have site visits to see the plant in action. Thus, successful German technology is also transferred abroad.