It is the activation process which accounts for the lion‘s share of the electricity used in the treatment of wastewater. In energy studies, it is worth taking a closer look at the processes, especially in this case. Armin Meister, and his engineering office, rely on dynamic modelling methods from system theory for the analysis and optimisation of existing systems in wastewater treatment plants. With this structured approach, the physics engineer at the wastewater treatment plant in Bingen has succeeded in significantly reducing the energy requirement through conceptual changes, and the use of modern hybrid blowers from AERZEN. At the same time, the plant‘s elimination performance has increased dramatically.
- Article Efficiency gains through modelling
Wastewater technology
The biggest leverage is process improvement
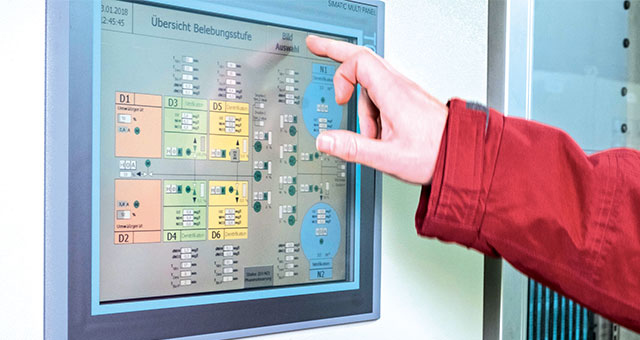
Pushing processes and the environment forward through modelling: for the wastewater treatment plant in Bingen, which has been designed to cater for a population equivalent of 80,000, this far-reaching approach has led to a considerable improvement and stabilisation of the cleaning performance. The energy savings in the area of activating sludge are divided between conceptual improvements, and the use of better machine technology. “Besides staff costs and maintenance costs, energy costs and discharge values also determine our operating costs,” says Meister. Lower discharge values mean a reduction in the wastewater levies which have to be paid to the national government. Investments therefore pay off twice.
The optimised processes require careful technical design, so that systems can be run as continuously as possible at the optimal load point with the aid of a fast and dense network of sensors. Meister investigated load curves spanning several years, and based on this he designed the modelling. The modelling forms the basis for defining future requirements for the compressor stations. “This made it possible to select the most suitable assembly in terms of energy consumption and overall cost-effectiveness, while ensuring the appropriate technical requirements for wastewater treatment and the necessary redundancy.” This led to the selection of AERZEN rotary lobe compressor, type Delta Hybrid. Here, two air conveying processes are combined in one machine: Root’s principle as full pressure compression for low pressure, and the screw compressor principle with internal compression for higher pressure. Calculations show that the rotary lobe compressor requires up to 15 percent less power than conventional compressors for absolutely oil-free air conveying.
Operation at optimal load point
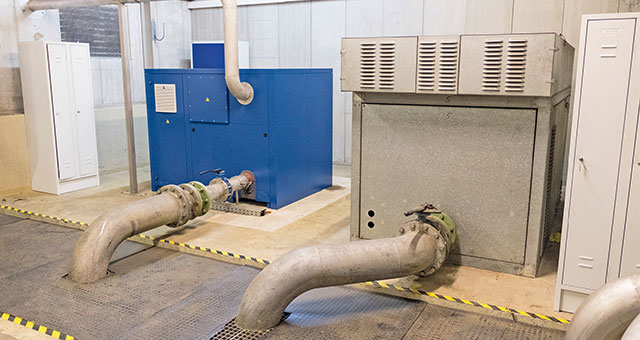
Four Delta Hybrid machines are required, which cover almost 90 percent of all operating cases, so that the older and less energy-efficient assemblies are only used for rare high-load or redundancy events. In view of the optimal load points, the rotary lobe compressors with graduated capacities and correspondingly adapted motor sizes are used for two independent compressed air systems.
The largest Delta Hybrid rotary lobe compressor, type D62S, with 110 kW motor rating and 1,000 mbar maximum differential pressure, supplies up to 3,500 cubic metres per hour. The D36S, D24S and D12S models are smaller dimensioned and deliver 2,150, 1,390 and 690 cubic metres per hour with motor ratings of 75, 55 and 30 kW respectively. The two smaller assemblies are installed in the engine house, which also houses the older machinery. The two large Delta Hybrid machines are located outdoors. A simple roof protects them from the weather.
Robust design for outdoor use
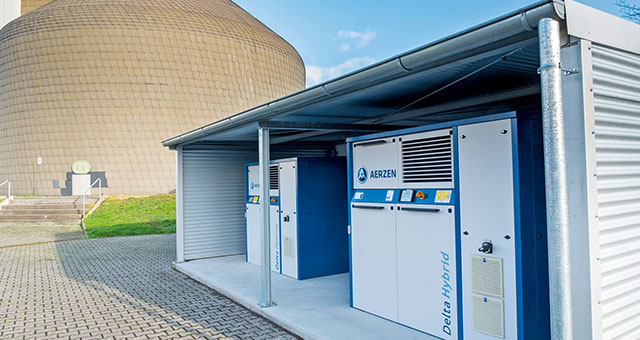
The decision to install the two Delta Hybrid, types D62S and D36S, outdoors, was made for two reasons: not enough available space and inadequate ventilation in the engine house. The Joule-Thomson effect, which occurs during air compression, means that the compressed gas mixture heats up, as the molecules move closer together due to the higher pressure. An increase of 100 millibars results in a temperature delta of +10 degrees centigrade. This increases the required compression effort due to reduced air density and lower oxygen content of the intake air. Installed outdoors, the Delta Hybrid machines can dissipate heat losses much more effectively into the environment and in turn suck in air that is not thermally preloaded.
This correlation has the same effect on energy efficiency as the use of technology tailored to performance. One aspect to consider at this point: the operation of the rotary lobe compressors with a frequency inverter for demand-oriented and thus economical speed control of the drive motor. The four sizes of the Delta Hybrid with their scaled motor rating also make it possible to operate the load points most frequently occurring with optimal efficiency. In addition, the high adjustment range of the Delta Hybrid machines ensures that there are large areas of overlap between the assemblies. These areas are necessary, in order to ensure optimal adjustment of all operating points and stable compliance with the control specifications, even in case of continuous load changes of the system. This is particularly important as the activator basins of the Bingen wastewater treatment plant are not divided into fixed zones for ammonium degradation and nitrification. Rather, the areas of the different biodegradation processes can be variably adapted to the contamination loads by connecting the basin zones and the precise air control of the surface ventilators mounted on the basin floor.
The areas into which air can be brought, and in what quantity, can be adjusted as required by means of control valves. There is a sliding pressure control system, so that valves, that are closed too far, do not cause the back pressure in the supply pipe to rise. This is based on the optimal interaction of volume flow, flap position and pressure. “Throttles, which are closed too far simply waste energy. 100 millibar more pressure means 20 percent more energy consumption,” the planner explains. “When it comes to improving the quality of a plant, precise, stable control methods, which are tuned to the speed of the coupled processes, are indispensable,” he adds.
In Bingen, a multi-stage control process operates in the background with pressure control as the leading variable for the compressor adjustment, and with a delay time of about half a minute. The control of the oxygen concentration in activation zones with settling times of about 10 to 15 minutes, which act on the control valves in the compressed air supply, is time decoupled from this. Their position ensures continuous adjustment of the system pressure and thus triggers the above mentioned sliding pressure control.