Heat Recovery Concepts from AERZEN
Sustainability and efficiency are indispensable in the industry. Today, they undoubtedly number among the most important challenges facing system manufacturers and operators. By its very nature, however, the generation of process air requires a relatively high amount of energy. A large quantity of heat energy, known as process heat, is released in the process. It arises not only in the generated airflow, but also under the acoustic hood due to heat loss from the motor, silencer and compressor. In the past, it frequently went unused.
As a manufacturer of high-performance compressors, AERZEN has long developed innovative solutions for putting this heat energy to practical use. As a result, the company offers plant operators cutting-edge compressed air technology and right-sized systems for heat recovery from a single source
The potential savings that could result from installing a heat recovery system are immense: up to 85 percent of the heat energy can easily be used for other operations, such as water heating, drying processes or preheating burner air. Energy losses, such as those caused by venting the heated air outside, are avoided. Heat recovery therefore means targeted, resource-saving energy conservation.
The investment costs for a heat recovery system are relatively low and are quickly compensated for by the energy savings. Older plants as well can be retrofitted and optimised without spending a lot of time and money. AERZEN is happy to help you implement individual solutions. Heat recovery can be implemented for a broad range of processes and uses:
- Supplying central heating systems
- Warm-air heating
- Sludge drying
- Warm air for processing tasks (e.g. drying processes in production)
- Producing hot water for showers and washrooms
- Heating service water for cafeterias
- Constructing thermal brakes
- Heating swimming pools.
The goal of every plant designer is to reduce costs by making the most efficient use possible of the energy introduced into a process. In the area of compressed air production, heat recovery is a simple way of meeting this challenge. To understand why a working compressor generates heat energy and how that energy can be used, it is useful to look at the operating principle of an air compressor:
Operating principle of compressors: Heat sources and options for recovering heat
The large quantity of waste heat produced when compressed air is generated says nothing about the efficiency of the machine. It is a by-product that necessarily arises when generating process air. Plant operators have long not been aware of the massive energy potential contained therein. As a rule, the heat is generated in two different ways: on the one hand, from compression of the medium by the assembly and on the other, by the waste heat (cooling air) from the motor, stage and silencer and the exhaust air from the oil cooler.
Compression
Machines such as screw compressors and positive displacement blowers compress the sucked-in surrounding air by means of screws or rotary pistons. This form of air compression is a thermodynamic process that heats the sucked-in medium, for example, air or gas. From a physical standpoint, the process converts electrical energy into heat energy. When compressors are used, the process gas may reach temperatures as high as 280°C.
The logical approach to recovering heat from process air is to use heat exchangers; when heat exchangers are integrated into the airflow, a medium such as water can flow through them and be heated to a preset temperature, simultaneously removing heat from the airflow. The heated water can be reused as process or service water or fed into the central heating system. AERZEN offers precisely designed heat exchangers for this purpose, that convert the maximum amount of transferable heat with minimal pressure loss.
Cooling air (heat radiation)
Additional heat energy is created under the acoustic hood of the assembly by the radiation of the motor, oil cooler, compressor stage, rotary piston stage, piping and silencer. This strongly heated cooling air can be put to practical use as well. The heat can be consolidated in the exhaust air ducts integrated in the assembly and transported as heating air to adjoining rooms or workshops. A temperature-controlled outlet can regulate the airflow, so that a uniform ambient temperature is achieved. If no heating is required in summer, for example, the excess heat can be conducted outside.
Heat recovery in wastewater treatment
Wastewater treatment is a core sector of Aerzener Maschinenfabrik. The family-owned company is a global player in this area and is continuously developing resource-saving and environmentally friendly all-in-one solutions for customers all around the world. This includes not only the selection of ‘custom-fit’, optimal machine technology, but also concepts for recovering heat. In wastewater treatment plants, the assemblies are normally used to aerate the aeration tanks. In the process, an airflow with a pressure of approx. 1 bar is generated by AERZEN positive displacement blowers, turbo blowers and compressors working jointly or as individual assemblies. The airflow is pumped into the aeration tanks (the ‘biology’ of the plant). The oxygen contained in the air plays a decisive role in an important step in the process: biological sewage treatment.
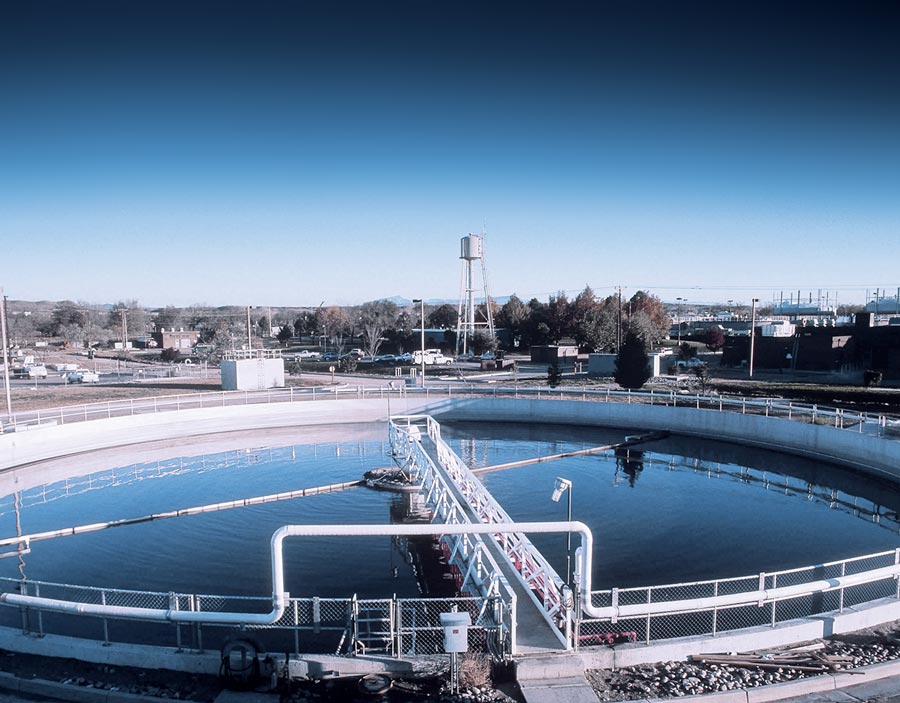
Measured in terms of the total energy costs for a wastewater treatment plant, airflow generation naturally accounts for the largest percentage. The potential for savings in this area is therefore especially high. The possibilities are vast: just one compressor with a rating of 22 kW can meet the heating needs of a single-family home.
Aerzener Maschinenfabrik’s many success stories show how the energy balance of a wastewater treatment plant can be markedly improved by implementing heat recovery solutions and choosing the optimal machine technology for each application. You can find several examples here:
Another example of highly efficient heat recovery implemented in cooperation with AERZEN can be found at the Essen-Kupferdreh wastewater treatment plant. The plant uses four positive displacement blowers to supply air to the aeration tanks. Thanks to the installation of a tube bundle heat exchanger, the plant now makes practical and efficient use of the waste heat from the blowers. The converted energy from the component now supplies heat energy to the heating system and the buffer tank for warm water. The resulting savings are colossal: heat recovery alone enables the plant in Essen-Kupferdreh to save more than 30,000 euros each year.
At the Wertach wastewater treatment plant in Bavaria, it was possible to forgo the installation of a new burner for heating boiler water, thanks to the use of a heat exchanger. In Wertach, two Delta blowers with fixed speeds are used for the basic workload. When the requirements are higher, for example, during the season when hikers and skiers visit in large numbers, a third blower with a variable speed is activated.
The warm, 68°C air generated by the compression process is cooled to under 30°C by an air-water plate heat exchanger. The resulting delta of almost 40°C can thus be used to store the boiler water of the heating system. The heat exchanger integrated in the system is equipped with flow-optimised profiles and causes almost no pressure loss in the process air flow.
If no heating is needed (e.g. in summer), it is easily switched off. A mechanical valve in the piping enables some or all of the air to be routed directly to the aeration tanks instead of through the heat exchanger, thus making demand-driven control and heat recovery possible at all times. In Wertach, heat recovery made it possible to save approx. 1,850 litres of fuel oil per year. You can find more information on the subject in the article entitled ‘Efficient heating with lost heat’ in our customer magazine.
To conform with strict environmental requirements at the Filderstadt-Bonlanden wastewater treatment plant, which was built in the 1960s in the German state of Baden-Württemberg, four Delta Hybrid rotary lobe compressors were equipped with a heat recovery system as part of a modernisation and renovation project in cooperation with AERZEN.
The combination of assemblies provides 100% oil- and absorbent-free compressed air for the aeration of the aeration tanks in a highly energy-efficient manner. The oil and absorbent-free operation means not only savings on service and maintenance, but also improved process reliability for the plant. Once the modernisation measures were complete, the system began circulating the machine-warmed ambient air via an extraction system and using it to heat other engineering rooms.
But the biggest savings were achieved by fitting a tube bundle heat exchanger into the main pipeline of the system. In the heat exchanger, heat is removed from the process air flow and used to heat water. As a result, water heating costs could be eliminated altogether. You can learn more about heat recovery in Filderstadt-Bonlanden from our customer magazine in an article entitled ‘Every kilowatt put to optimal use’.
Heat recovery in pneumatic conveying
Pneumatic conveying involves the transport of bulk goods such as flour, powder, sand or cement with the help of air. It is used in many industries, such as food processing, bulk goods, chemicals and materials. To create the required airflow, AERZEN compressors, blowers and rotary lobe compressors are often used. Very high outlet air temperatures can be achieved in the process.
The ambient air, which usually has a temperature of approx. 20°C, is sucked in and can reach temperatures of up to 280°C due to the compression process, for example, in an application involving screw compressors. To prevent the transported bulk goods from being damaged by the high temperatures, the process air often has to be cooled back down. The heat can be removed from the compressed air with the help of a heat exchanger and used for heating, water heating or process heat. Depending on the design, the pressure loss caused by the installation of a heat exchanger is 1-3% in relation to the absolute intake pressure in the aftercooler. The resulting increase in the drive output of the motor is nominal compared to the amount of energy saved by the heat exchanger.
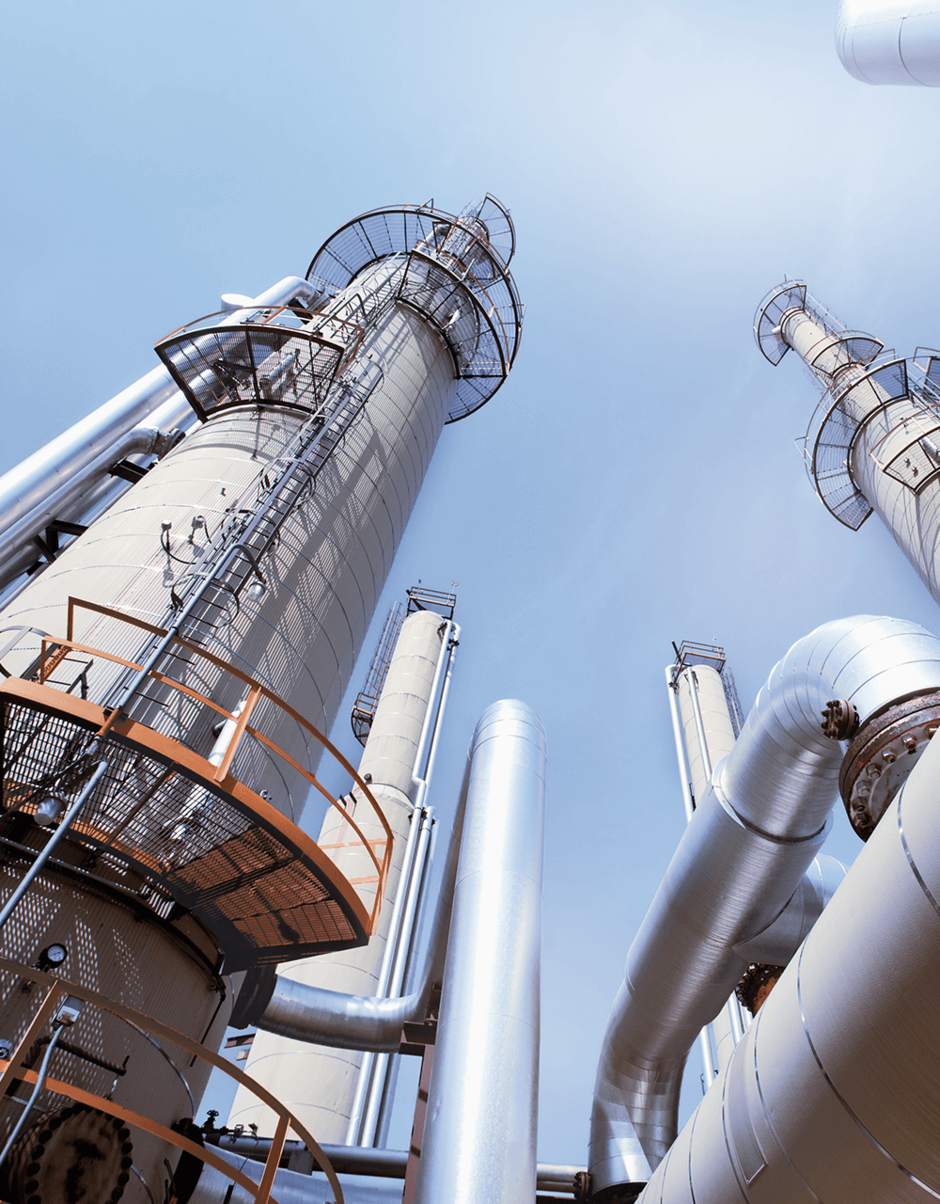
When does it pay to recover heat?
Several factors should be considered before deciding to procure a heat recovery solution.
To begin with, the structural conditions should be checked. It is important that the waste heat source and the heat sink be positioned close together. If they are too far apart, the plans should factor in energy losses due to transport and higher costs for piping. If it takes a lot of effort to transport or store the heat, higher investment costs have to be reckoned with. Furthermore, there must be a Δ T of at least 5-10 k between the plant’s waste heat source and heat sink in order for a heat recovery installation to pay off.
In general, it could be said that heat recovery is especially beneficial when used with large assemblies and constantly running production processes. But a heat recovery system can also pay off in cases where the waste heat is lower but the workload higher. In principle, heat recovery is more profitable the more continuously the assemblies remain in operation.
Summary
The large amount of energy required to generate compressed air can be recovered and used in various ways. With AERZEN technologies and expertise, new projects in the areas of wastewater treatment and pneumatic conveying can be designed to make use of heat energy for heating rooms, halls or water (process or service water) or for steps in the production process. Many different applications are possible.
Existing plants can also be modernised using simple means that increase their efficiency. In this field, AERZEN offers its customers a broad portfolio of services, for example, a 24-hour telephone information service, a machine diagnosis and the AERaudit, in which service employees develop a plan for modernising a plant.
And with the help of AERZEN’s Room Ventilation Calculator, engineers and wastewater treatment plant owners can find a suitably designed heat exchanger for their plant themselves.